SME Supply Chain Management in South Africa
Efficient Supply Chain Management Boost Profits for SMEs: How to manage production
Enhance your business's competitiveness by focusing on efficient production and robust supply chain management. Streamline workflows, adopt cutting-edge technologies, and implement quality control measures to optimise your production processes. Evaluate key performance indicators for valuable insights into cycle time, defect rates, and resource utilisation, fostering continuous improvement.
Optimising Production Management for SME Supply Chain Success
Understanding the intricacies of production management is no longer a luxury but a necessity for SMEs aiming to thrive in an increasingly complex business environment. Effective production management encompasses a spectrum of crucial tasks, including resource allocation, inventory control, quality assurance, and scheduling. By mastering these aspects, SMEs can enhance operational efficiency, minimize costs, and accelerate time-to-market, thereby gaining a significant edge over competitors. Moreover, adept production management empowers SMEs to adapt swiftly to market fluctuations, seize emerging opportunities, and mitigate risks, laying a robust foundation for long-term success. This article delves into the pivotal role of production management in SMEs, offering insights and strategies to help businesses unlock their full potential and achieve sustainable growth in today's fiercely competitive marketplace.
Enhance SME Supply Chain Efficiency with Strategic Production Management
- Effective production management is crucial for businesses to ensure efficiency, cost-effectiveness, and timely delivery of goods or services. One key consideration is the optimisation of production processes. This involves streamlining workflows, eliminating bottlenecks, and adopting advanced technologies to enhance productivity. Businesses should invest in modern production systems, such as automation and smart manufacturing, to improve accuracy, reduce errors, and accelerate production cycles. Additionally, implementing robust quality control measures is essential to meet customer expectations and regulatory standards. Monitoring and analysing key performance indicators (KPIs) related to production, such as cycle time, defect rates, and resource utilisation, can provide valuable insights for continuous improvement.
- Another critical aspect for businesses to consider is supply chain management. A well-coordinated and resilient supply chain is essential for securing the necessary raw materials and resources for production. Businesses should assess and mitigate risks in the supply chain, such as disruptions caused by geopolitical events, natural disasters, or supplier issues. Adopting digital technologies for real-time visibility into the supply chain can help businesses make informed decisions and respond quickly to unforeseen challenges. Collaboration with suppliers and the establishment of alternative sourcing strategies can contribute to supply chain flexibility. Ultimately, businesses need to strike a balance between cost efficiency and resilience to create a production and supply chain framework that is adaptive and responsive to the dynamic business environment.
Supply Chain Management is about increasing efficiency by coordinating the efforts of the various entities in the supply chain. This can result in a business gaining a competitive advantage over its competitors and improving the quality of its products, both of which can lead to increased sales and revenue. This skills programme provides a platform and tools for entrepreneurs and business managers to develop and manage supply chain management system.
How to manage production
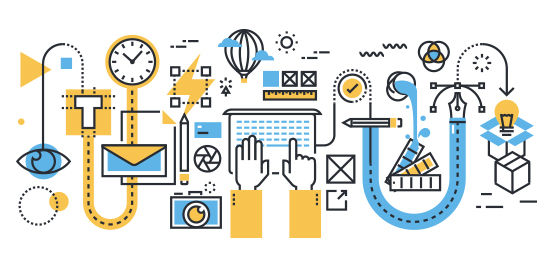
Written by: Malose Makgeta
MBA with 20+ years experience in SME development and funding. LinkedIn Profile
Production Management Best Practices - Entrepreneurship Lessons from Movies The Founder, War Dogs and Moneyball
- The Founder (McDonald's): The McDonald's brothers, Richard and Maurice McDonald, and Ray Kroc exemplified effective production and operational management in the success of McDonald's. The brothers initially developed the "Speedee Service System," an innovative approach that streamlined kitchen processes, emphasising speed, consistency, and efficiency. This included the assembly line concept in the kitchen, simplifying menu offerings, and implementing a fast-food model. Ray Kroc, recognising the potential of their system, played a pivotal role in scaling the business. His contribution was in standardising operations, franchising, and implementing rigorous quality control across McDonald's outlets. This standardised approach allowed for consistent product quality and operational efficiency throughout the expanding franchise, showcasing a successful application of optimised production processes and supply chain management in the fast-food industry.
- War Dogs (AEY): In the movie "War Dogs," AEY, led by Efraim Diveroli and David Packouz, managed production by leveraging a network of international suppliers to fulfill their U.S. military contracts. Facing challenges such as tight deadlines and complex logistics, AEY adopted a dynamic and resourceful approach. They navigated the global arms market, sourcing weapons and ammunition from various countries to meet the demands of their contracts. The company relied on strategic partnerships and negotiations to secure deals and ensure a steady supply chain. AEY's management of production showcased their adaptability and willingness to exploit opportunities in the international arms trade, even as it led them into morally ambiguous and legally questionable territory.
- Moneyball (Oakland A's): Billy Beane, faced with budget constraints compared to larger-market teams, strategically focused on optimising player performance metrics rather than relying on conventional scouting methods. This involved a meticulous analysis of key statistics (KPIs) to identify undervalued players who could contribute significantly to the team's success. Similar to the emphasis on streamlining production processes, Beane aimed to create a cost-effective and efficient team by redefining the criteria for player selection. By embracing data-driven decision-making and challenging traditional norms, the Oakland A's, under Beane's leadership, exemplified how a strategic emphasis on optimisation and efficiency in player selection could yield competitive advantages and success within the constraints of a limited budget.
CONTEXT
Business plan development is the process of creating a business strategy and plan to help a business implement its vision and achieve its goals over time. The primary goal of business plan development is to create a strategy for moving a business from its current state to its desired state through a series of business actions. The skills programme provides entrepreneurs and business managers with a platform and tools for business strategic planning.
Description
Production management is the process of controlling a businesss operations so that the outputs of desired goods and services are produced. It entails organising, carrying out, and managing processes that transform raw materials into finished products and services. As a result, it is possible to state that product management is concerned with
Purpose
Be able to understand the role and function of production and operations management, selected design, planning, and control tasks and responsibilities of production and operations managers, and productivity management in the context of organisational operations management.
Rational
Production management reduces production costs and maximises resource utilisation. A concise blueprint allows for the efficient use of resources and time, reducing the gap between the production process and the output. Evaluation of production processes and maintenance downtime will ensure that processes can be managed efficiently, optimising workforce efficiency. A well-thought-out production function will result in high-quality products, a faster rate of production, and a lower cost per unit.
Key Lessons
Click here and draft your business plan in minutes
To request tailored accredited training and enterprise development services, contact us at businessplan@superdealmaker.com.
Get List for Funding Opportunities in Minutes, Click Here
To request tailored investment banking services, contact us at businessplan@superdealmaker.com.
Mastering Production Management - The McDonald's Production Symphony: Efficiency in Every Fry
Let's dive into the sizzling world of McDonald's, where the management of production isn't just a task; it's a symphony. Picture this: the year is 1954, and the McDonald brothers revolutionise the fast-food industry by introducing the Speedee Service System. Now, let's unravel the secrets behind the scenes, where efficiency isn't just a goal; it's a way of life.
The golden arches aren't just a symbol; they represent a well-oiled machine of production. The McDonald's assembly line, inspired by the principles of efficiency expert Ray Kroc, redefined how fast food was made and served. Every task was broken down into simple, repeatable steps. Burgers flipped, fries fried, and shakes shaken with a precision that rivaled a choreographed dance. For instance, the assembly line approach meant that each employee had a specific task—whether it's flipping patties or assembling burgers, everyone had a role, and the result was a seamless, high-speed production process.
The impact of McDonald's production management was nothing short of revolutionary. By streamlining operations and maximising efficiency, they not only served burgers but also served as pioneers in the fast-food industry. The iconic "fast" in fast food wasn't just a promise; it was a reality born out of meticulous production planning. This not only reduced waiting times for customers but also set a benchmark for the entire industry.
Efficiency at McDonald's wasn't just about speed; it was about maintaining quality. The precision in the production process ensured that each burger, fry, and shake met the same high standards, regardless of the location. For example, the use of standardized procedures, such as the exact amount of condiments on a burger or the precise cooking time for fries, showcased how McDonald's maintained consistency and quality across its vast network of restaurants.
As entrepreneurs, take a cue from the golden arches. Efficient production isn't just about speed; it's about creating a symphony where every note, or in this case, every task, contributes to the harmony of success. The impact of McDonald's production management is not just etched in the history of fast food; it's a lesson for businesses across industries – the art of turning efficiency into an iconic legacy.
Production Management Insights for SME Supply Chain Leaders
Production is an activity that adds value to a material by utilising a range of capabilities, enabling a variety of uses for that material. Value is added at every stage of the production process. The earliest producers were probably lone artisans who designed and produced goods. They worked as both a manufacturer and a supplier, gathering and managing the resources and putting different processes to use to enhance the materials' value. production evolved over time to include a variety of specialists, each of whom provided or added particular types and amounts of value.
Production management is the process of planning, organising, and controlling the activities involved in the production of goods or services. It focuses on efficiently utilising resources to meet customer demand while minimising costs and maximising productivity. Production management is the process of controlling a business's operations so that the outputs of desired goods and services are produced. It entails organising, carrying out, and managing processes that transform raw materials into finished products and services. As a result, it is possible to state that product management is concerned with
The goal of production management, also known as operations management, is to ensure a seamless production process through effective planning and control of business operations The business transforms raw materials by using equipment, labor, or other external forces to create something new, which is at the core of the supply chain management process. Despite not being the last step in the supply chain management process, this final product is what the production/production process ultimately aims to produce.
Production management plays a crucial role in coordinating the flow of materials, information, and resources across various stages of the production process. It involves tasks such as demand forecasting, capacity planning, scheduling, inventory management, quality control, and continuous improvement.
Sub-processes within the production process, such as assembly, testing, inspection, or packaging, may be further broken down. A business must be aware of waste and other manageable factors during the production process that could lead to changes from the original plans. For instance, a business must address the problem or go back to the earlier stages of SCM if it finds that it is using more raw materials than it had anticipated and sourced.
Naturally, raw materials are a necessary part of the production process, but they are not the only one. Without labor inputs, you are left with a pile of materials, such as fabric that needs to be sewn into clothing, wood that needs to be built into furniture, and metal that is useless until it is engineered into machinery. To ensure that the people building the products are aware of the parts and assemblies that are available to them and are kept up to date on usage, a supply chain management team collaborates closely with designers and engineers.
The goal of production management is to ensure that production operations are carried out smoothly and efficiently, from sourcing raw materials to delivering finished products to customers. By effectively managing production processes, companies can reduce lead times, optimise inventory levels, improve product quality, and enhance customer satisfaction.
Overall, production management in supply chain management is essential for achieving operational excellence and gaining a competitive advantage in today's dynamic business environment.
Types of Production Management
There are several types of production management practices commonly used in supply chain management:
- In this approach, products are manufactured based on demand forecasts and stocked in inventory before customer orders are received. It allows for faster order fulfillment but carries the risk of overstocking or stockouts if demand predictions are inaccurate.
- Make-to-Order (MTO): With this strategy, products are manufactured only after receiving customer orders. It offers greater customisation and minimises the risk of overstocking, but may result in longer lead times and production delays.
- Assemble-to-Order (ATO): ATO involves assembling products based on predefined configurations or options once an order is received. It offers a balance between customisation and lead time reduction by pre-manufacturing common components and finalising assembly upon order confirmation.
- Engineer-to-Order (ETO): ETO is characterised by the production of highly customised products that are designed and engineered specifically to meet individual customer requirements. It involves significant collaboration between the customer and the manufacturer to develop unique product specifications.
- Just-in-Time (JIT): JIT production management focuses on producing and delivering products exactly when needed, eliminating excess inventory and waste. It relies on close coordination with suppliers, efficient production processes, and real-time demand information to achieve lean and efficient operations.
- Lean Manufacturing: Lean production management emphasises the elimination of waste across the entire production process. It involves identifying and eliminating non-value-added activities, optimising resource utilisation, and continuously improving efficiency through practices such as Kaizen and Kanban.
- Total Quality Management (TQM): TQM focuses on achieving high product quality by involving all employees in quality improvement efforts. It emphasises continuous monitoring, defect prevention, customer feedback incorporation, and adherence to rigorous quality standards throughout the production process.
- Six Sigma: Six Sigma is a data-driven approach to quality management that aims to minimise defects and process variations. It involves using statistical analysis and problem-solving methodologies to improve process performance and achieve near-perfect quality levels.
These various types of production management approaches can be applied depending on the nature of the products, customer requirements, market demand patterns, and organisational capabilities.
The function of production management is to find the perfect balance:
- Right quality
- Right quantity
- Right time
- Right cost
Types of Production Processes
- Repetitive manufacturing - This production/assembly line operates around-the-clock thanks to the use of manufacturing process automation tools like robotics and conveyor belts.
- Discrete manufacturing - This also depends on production lines. However, the manufacturer produces a variety of goods, necessitating the setup and modification of the production line according to the goods being produced.
- Job shop manufacturing - The manufacturing process management strategy preferred by the small manufacturer, which makes use of workshops and distinct production facilities to enable custom products.
- Batch production - In order to meet customer demand, manufacturers can produce products in as many batches as necessary.
- Continuous production - While dealing with raw materials like gases, liquids, powders, or slurries, including those from the mining industry, another manufacturing process operates round-the-clock.
Operations Management
Similar to production management, operations management is the day-to-day management of the business, ensuring that operations and production are carried out effectively and without hiccups. This includes handling administrative, factory-level, and service management.
The customer is your operations management's main point of focus. If the client is happy, you are moving in the right direction. However, operations management also deals with how you manage your resources because you want to increase customer satisfaction while wasting as little as possible and making the best use of your available resources. But what are the roles that operations management plays?
- Strategy - To gain a competitive advantage over your rivals, you'll need to develop plans and strategies under operations management that will help you achieve lean inventory and a smooth production flow, from raw inventory management to routing manufacturing.
- Designing products - Here is where you should look into whether your product satisfies consumer demand and reflects current market trends. Although your product may have made it past the prototype stage, you still need to be prepared to modify it in light of shifting trends and forecasts.
- Forecasting - Demand Planning will enable you to comprehend how your product is performing in the market and decide how to proceed, be it by increasing, decreasing, or even stopping production on a product. And that's the ins and outs of operations management. As you can probably see, there isn't much of a difference between operations management and production management. Here are some reasons why it's crucial to have your operations and production management down to a science, regardless of whether you find it difficult to distinguish between the two or choose to call it something else.
Difference Between Production and Operations Management
The term "production and operations management" is all-inclusive and refers to overseeing the creation of your products as well as those finished goods and services.
Traditionally, a manufacturer would produce its goods, send them to a third party, and that would be it. But as more companies regain control over their name and reputation, they have begun to offer services like customisation in their products.
The distinction between production management and operations, products and services, has gotten increasingly hazy as manufacturers have shifted toward a direct-to-consumer brand and even retailers now produce their own branded products. Do you remain perplexed? Operations management and production management are very similar, but the following is where they diverge:
- Production management is the supervision and control of product production.
- Operations management: The work necessary to complete the production as well as the services provided to the customer.
Functions of Production Management
To better meet customer needs, production management makes use of the 6Ms: Men, Machines, Money, Methods, Materials, and Market. Its primary objective is to produce goods and services in the appropriate quantities, with the best possible quality, on time, and at the lowest possible cost. Adopting new technologies and cutting-edge workplace changes is made simple by production management. In order to ensure that the desired output is produced, production management is responsible for supervising and controlling all employees who are involved in the business's production processes.
- Product and design selection - Production management assists the organisation in selecting the appropriate product for production as well as selecting a suitable design for the product. It has become critical for organisations' survival to have a good understanding of their consumers in order to create products that fully satisfy needs. Products must be thoroughly evaluated in order to meet customer needs while remaining cost-effective.
- Production planning and control - Choosing the best manufacturing processes for a specific product is also critical. Decisions must be made in order to select the appropriate type of machine and technology, the amount of capital required, and so on. It entails planning ahead of time. Decisions such as production quantity, process flow, and so on are all planned. The term "routing" refers to the process of charting out the sequence of operations for a smooth workflow. The production manager is in charge of quality control. The actual process is compared to the blueprint so that any deviations from the original plan can be mapped out and any loopholes in the original plan can be identified and corrected.
- Maintenance and replacement of machinery - Production management is in charge of the maintenance and replacement of machines and equipment to ensure that production processes run efficiently and smoothly. The production manager and team handle this to avoid speed breaks and production halts.
Operations Strategy
A clear operations strategy is one of the most practical tools for keeping your team on track with the goals of your business. When a business has a solid operations strategy in place, it is easier to introduce new products and services and respond to market demands while measuring the impact on employees and resources. An operations strategy must include the following elements:
- Define how products are created (or services are delivered) at a low cost while adhering to SMART goals.
- Describe how products are manufactured to a standard specification.
- Describe how services are delivered with known quality and without error.
- Define the steps taken in response to market demands.
- Define how products and services should be delivered to meet the needs of customers (matching a quotation or brochure description, for example)
- Describe how the business should incorporate flexibility into its daily operations, such as changing the volume or speed of production, or the mix of products or services delivered.
Lean Integration Principles
The principles of Lean Integration may appear similar to those of Six Sigma at first glance, but there are some significant differences. Six-Sigma is an analytical technique focusing on quality and defect reduction, whereas Lean is a management system focusing on delivering value to the end customer by continuously improving value delivery processes. By focusing on critical customer requirements, Lean provides a solid framework for improving efficiency and effectiveness.
- Focus on the customer while eradicating waste: All activities that do not add value for the customer should be carefully examined, eliminated, or reduced. Waste elimination should be approached from the customer's perspective. The customer in an integration context is frequently a department or group within a company that makes use of, benefits from, or pays for the integrated capabilities.
- Continuously improve: To stimulate innovation and continually enhance the end-to-end process, a data driven cycle of hypothesis-validation-implementation should be used. A related idea that aids in the establishment of this principle is adopting and institutionalising lessons learned and maintaining integration knowledge.
- Empower the team: Creating cross-functional teams and sharing commitments across individuals empowers teams and individuals who have a clear understanding of their roles and the needs of their customers. Senior management also encourages the team to experiment with new ideas and innovate without fear of failure.
- Optimise the whole: Take a big-picture view of the end-to-end process and optimise the whole to maximise customer value. This may necessitate performing individual steps and activities that appear sub-optimal when viewed in isolation but aid in streamlining the end-to-end process.
- Plan for change: Using mass customisation techniques such as automated tools, structured processes, and reusable and parameterised integration elements reduces cost and time in both the build and run stages of the integration life cycle. Another important technique is a middleware services layer, which provides applications with persistent data abstractions via standardised interfaces, allowing the underlying data structures to change without affecting the dependent applications.
- Process automation: Task automation improves the ability to respond to large integration projects as well as small changes. Automation, in its ultimate form, removes integration dependencies from the critical implementation path of projects.
- Quality is built in rather than inspected in: Process excellence is emphasised, and quality is built in rather than inspected in.
The McDonald's Magic: Cracking the Code on Production Efficiency
Ever wondered how McDonald's manages to serve millions of customers with lightning speed and unwavering consistency? Enter the realm of production efficiency, a realm where the McDonald's brothers, Ray Kroc, and their innovative Speedee Service System shine. The brilliance lies in the assembly line approach, where each station is dedicated to a specific task. For instance, the "shake machine" ensures a consistent product, while the "grill station" maintains precision in cooking times. This meticulous division of labor not only ensures speed but also guarantees uniform quality across all outlets.
McDonald's production strategy revolutionised the fast-food industry. Take the iconic Big Mac as an example. Its construction is a symphony of efficiency – the "special sauce" is precisely dispensed, lettuce is shredded uniformly, and patties are grilled to perfection. This orchestration not only satisfies hunger in record time but also ensures that whether you're in New York or Tokyo, your Big Mac experience remains consistent. The impact? An unparalleled level of customer satisfaction and loyalty that has endured for decades.
So, what can entrepreneurs glean from the McDonald's production playbook? The key takeaway is meticulous organisation. Just as each station in a McDonald's kitchen has a specific role, a business should have clearly defined processes. Efficiency comes from streamlining tasks and reducing unnecessary complexity. Embrace technology where it can enhance precision, and remember, a well-orchestrated production system isn't just about speed; it's about consistently delivering a quality product that keeps customers coming back for more.
SME Supply Chain Optimization: The Power of Production Management
A strong operations strategy can lead to greater consistency - which in turn delivers cost-efficiencies back into your business - as long as it closely reflects the practical decision-making that is required in your business.
Effective production management in supply chain management is crucial for several reasons:
- Meeting customer demand: By implementing efficient production management practices, organisations can ensure that customer demand is met in a timely manner. This leads to higher customer satisfaction and loyalty.
- Optimising resource utilisation: Efficient production management helps in optimising the use of resources such as raw materials, labor, and equipment. This minimises waste, reduces costs, and improves overall productivity.
- Reducing lead times: By streamlining production processes, organisations can significantly reduce lead times, allowing them to respond quickly to customer orders and market fluctuations. This enables faster order fulfillment and enhances competitiveness.
- Improving product quality: Effective production management includes robust quality control measures, ensuring that products meet or exceed customer expectations. This leads to higher customer satisfaction, fewer returns or rejections, and a positive brand reputation.
- Enhancing supply chain coordination: Efficient production management facilitates better coordination and collaboration with suppliers, enabling synchronised production schedules, reduced inventory holding costs, and improved overall supply chain performance.
- Enabling cost savings: By optimising production processes and minimising waste, organisations can achieve cost savings in areas such as inventory holding costs, labor costs, and production downtime.
- Driving continuous improvement: Effective production management fosters a culture of continuous improvement, encouraging organisations to identify areas for enhancement, implement process refinements, and strive for operational excellence.
- Gaining a competitive advantage: Organisations that excel in production management within the supply chain can gain a significant competitive advantage. They can offer faster delivery, higher quality products, and more efficient operations, setting themselves apart from competitors.
In summary, effective production management in supply chain management enables organisations to meet customer demand, optimise resources, reduce lead times, improve product quality, enhance supply chain coordination, achieve cost savings, drive continuous improvement, and gain a competitive advantage in the market.
Other Benefit of Production Management
- Effective use of capital and resources - Production management reduces production costs and maximises resource utilisation. A concise blueprint allows for the efficient use of resources and time, reducing the gap between the production process and the output. Evaluation of production processes and maintenance downtime will ensure that processes can be managed efficiently, optimising workforce efficiency. A well-thought-out production function will result in high-quality products, a faster rate of production, and a lower cost per unit.
- Competitive advantage - Production management can be a valuable tool for businesses facing market competition. A more efficient flow of processes increases efficiency while allowing the business to provide quality products and services. Production management techniques aid in the effective innovation of new products and the development of new and high-quality products. It can help organisations become market leaders because less time spent on production processes means more resources to devote to other areas that may require more attention.
- Minimises risk of product failures - Preparing a clear roadmap and gathering information and assumptions aids in market assessment and reduces the likelihood of failure. Knowing the market's requirements and needs will help reduce the chances of a product failing. Finally, product management, like everything else, cannot guarantee success, but it can reduce the likelihood of failure.
Benefits of Outsourcing
Outsourcing is the practice of hiring a third party from outside a business to carry out tasks or produce goods that were previously done internally by the business's own staff and employees. Companies typically engage in outsourcing as a means of reducing costs.
The following advantages of outsourcing:
- Improved focus, quality, and simplification of remaining in-house operations
- Lower cost production operations, including reduction of in-house inventories
- Shorter product realisation cycles (faster time to market) and lower product development costs if suppliers are directly involved in product design
- Access to capabilities and technologies that could not be readily developed or cost-effectively acquired
Lean integration is a management system that emphasises creating value for customers, continuous improvement, and waste elimination as a sustainable data integration and system integration practice.
Benefits of Lean Integration
The Lean integration practices turn integration from an art to a science, a repeatable and teachable methodology that shifts the focus from integration as a one-time activity to integration as a long-term activity that enables organisational agility.
- Efficiency: Continuous efforts to eliminate waste typically result in labor productivity improvements and lead-time reductions.
- Reusable components, highly automated processes, and self-service delivery models improve organisational agility.
- Data quality is improved, and data is transformed into a valuable asset.
- Governance: Metrics that drive continuous improvement are established.
- The use of a fact-based approach facilitates innovation.
- Staff Morale: Staff is kept engaged and motivated by high morale, which drives bottom-up improvements.
How to Implement Efficient Production Management: Leverage Production Management for Superior Business Supply Chain Results
Implementing efficient production management in supply chain management involves several key steps:
- Forecast demand: Accurately predict customer demand to ensure production aligns with market needs. Utilise historical data, market research, and statistical methods to generate demand forecasts.
- Optimise capacity: Determine the optimal production capacity to meet demand while avoiding underutilisation or overburdening. Analyze production capabilities, equipment efficiency, and workforce capacity to make informed decisions.
- Create production schedules: Develop detailed schedules that outline the sequence and timing of production activities. Consider factors like production lead times, resource availability, and order priorities to maximise efficiency.
- Manage inventory: Maintain optimal inventory levels by implementing effective inventory management techniques. Utilise just-in-time (JIT) principles, economic order quantity (EOQ) models, and regular inventory audits to minimise holding costs while ensuring timely availability of materials.
- Ensure quality control: Implement rigorous quality control measures to maintain high product standards. Establish quality assurance processes, perform inspections, and conduct regular quality checks throughout the production cycle.
- Enable real-time visibility: Leverage technology solutions, such as enterprise resource planning (ERP) systems and supply chain management software, to gain real-time visibility into production processes. This allows for better monitoring, tracking, and coordination of activities.
- Continuous improvement: Foster a culture of continuous improvement by encouraging feedback, analysing performance metrics, and implementing process enhancements. Embrace lean manufacturing principles, Six Sigma methodologies, and other improvement frameworks to drive efficiency and productivity gains.
- Collaborate with suppliers: Establish strong partnerships and collaboration with suppliers to streamline the supply chain. Foster open communication, share demand forecasts, and coordinate production schedules to minimise disruptions and optimise resource utilisation.
By following these steps, organisations can implement efficient production management practices in supply chain management, leading to improved operational performance, reduced costs, and enhanced customer satisfaction.
Creating an Operations Strategy
Strategy is one of the most overused words in any business planning session. A solid operations strategy, on the other hand, should ensure that your business can operate and succeed in any commercial situation. In short, an operations strategy explains the who, what, when, and how of a business's day-to-day operations. It supports your overall business goals and keeps you focused on SMART objectives and realistic targets.
When it comes to developing a practical operations strategy, one golden rule applies: simple is best. Begin by breaking down objectives into timeframes that seem attainable for your business's line of work. Explain your overarching goals - your mission, your vision, and what you want to accomplish as a business. Then consider the primary activities that could assist you in achieving those objectives. They could be:
- Production of a specific product
- Delivery of a particular service
- Use of a specific quality control
- A unique method of delivery
- A particular way of working
Of course, there are additional criteria. Whatever criteria seem appropriate, make sure you can define them precisely and select an accurate measure of their performance. These measures should become the key performance indicators (or KPIs) for your business to evidence and calculate success and failure over time.
Advanced Production Management Tactics: McDonald's Production Mastery
Stepping into the McDonald's production arena is like witnessing a perfectly orchestrated symphony. The founders, inspired by the need for speed and efficiency, revolutionised the fast-food industry. Picture this: the Speedee Service System, where each component of the production process was meticulously designed for maximum efficiency. From the assembly line approach in the kitchen to the streamlined ordering process at the counter, McDonald's set a new standard for fast, consistent, and high-quality food production.
Precision in production isn't just a fancy concept for McDonald's; it's the secret sauce that fueled their success. By standardising processes and focusing on speed, they not only met customer expectations but exceeded them. The assembly line approach allowed for quick turnaround times, ensuring that customers received their orders promptly. This commitment to efficiency not only satisfied hungry patrons but also set a benchmark for the entire fast-food industry.
The impact of McDonald's production efficiency is undeniable. It paved the way for a new era in the fast-food industry, influencing competitors and shaping consumer expectations. Fast, reliable, and consistent became the gold standard. Beyond the immediate operational benefits, this production mastery allowed McDonald's to scale rapidly through franchising, ensuring that every Golden Arches location delivered the same unparalleled experience.
Production Management Essentials for SME Supply Chain Competitiveness
The central takeaway regarding production management underscores the critical role it plays in the success of businesses. To thrive, organisations must prioritise the optimisation of production processes. This optimisation involves embracing modern technologies, implementing quality control measures, and constantly evaluating key performance indicators (KPIs). Streamlining workflows through automation enhances efficiency, reduces errors, and accelerates production cycles. The commitment to continuous improvement ensures businesses remain agile and adept at meeting evolving market demands while maintaining high-quality standards in their production endeavors.
Businesses can gain a competitive edge by concentrating on enhancing their production capabilities independently. By adopting innovative technologies and refining operational processes, companies empower themselves to navigate industry challenges effectively. The focus on optimising production not only bolsters efficiency but also contributes to cost-effectiveness. This strategic approach positions businesses to proactively respond to market dynamics, fostering resilience and ensuring sustained growth in a dynamic business landscape.
Join the Conversation: Share Your Thoughts on This Article
- No comments yet.
Add Your Comment Now!