How to Review and Improve Quality Management System: Optimise Your SME's Quality Management Systems
Learn effective strategies to enhance your SME's quality management systems and procedures. Discover expert tips on reviewing and improving your QMS to boost efficiency and ensure top-notch quality standards.
Elevate your business's quality management system (QMS) with actionable insights for independent review and improvement. Discover the key steps to conduct thorough QMS audits, ensuring alignment with industry standards and identifying areas for enhancement. Embrace a culture of continuous improvement within your organisation by utilising feedback mechanisms from stakeholders and implementing robust training programs.
|
Why SMEs Must Master Quality Management Systems
Investing in quality management systems (QMS) is paramount for small and medium-sized enterprises (SMEs) striving for excellence. Understanding how to review and improve these systems ensures not only compliance but also operational efficiency and customer satisfaction. Our guide delves into the significance of QMS for SMEs, highlighting the benefits of adeptly managing quality processes. Learn how to enhance your QMS to meet industry standards, boost productivity, reduce costs, and gain a competitive edge. Empower your SME with the knowledge and tools to streamline operations, foster innovation, and build a reputation for delivering high-quality products and services.
Mastering Quality: Efficient System and Procedures: Enhancing QMS for SME Success
- Reviewing and improving a quality management system (QMS) is vital for businesses seeking to enhance product or service quality and overall organisational efficiency. Firstly, businesses should regularly conduct comprehensive audits of their QMS to identify areas for improvement. This involves assessing adherence to quality standards, evaluating the effectiveness of processes, and identifying potential risks. Gathering feedback from stakeholders, including customers and employees, provides valuable insights into areas that may require attention. Continuous monitoring ensures that the QMS remains aligned with organisational goals and industry standards.
- Secondly, businesses should prioritise a culture of continuous improvement within their quality management processes. This involves setting up mechanisms for feedback, both internally and externally, and using this information to drive positive change. Establishing key performance indicators (KPIs) allows businesses to measure the effectiveness of their QMS and identify areas that need refinement. Training programs and ongoing education for employees are crucial elements, ensuring that the workforce is equipped with the necessary skills and knowledge to uphold and contribute to the quality standards set by the organisation. By fostering a commitment to quality at all levels of the organisation and utilising feedback loops for regular improvement, businesses can elevate their QMS to meet evolving customer expectations and industry benchmarks.
How to review and improve quality management system
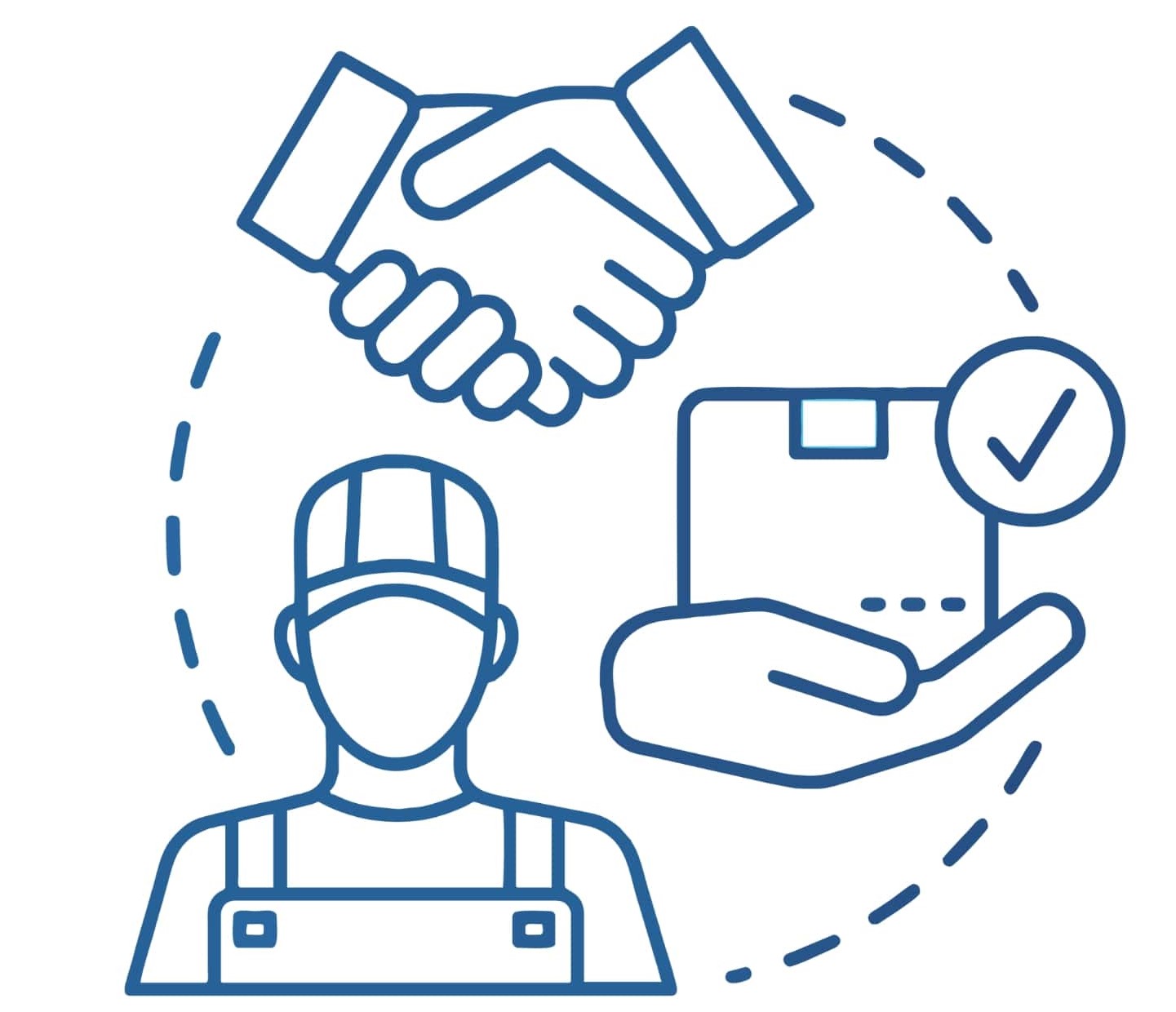
Written by: Malose Makgeta
MBA with 20+ years experience in SME development and funding. LinkedIn Profile
Review and Improve QMS - Entrepreneurship Lessons from Movies The Founder, War Dogs and Moneyball
- The Founder (McDonald's): The first restaurant opened by the McDonald brothers was not initially successful, leading them to redesign it into what we now recognise as McDonald's. Ray Kroc, who joined later, hadn't perfected the initial business model, nor did he have a detailed business plan. Both the McDonald brothers and Ray faced near failure because they lacked a business plan. Fortunately, they had the resources to delve deep into the business without one. If you have the resources, you can start without a business plan; otherwise, a business plan is critical.
- War Dogs (AEY): there is limited explicit focus on AEY (the arms dealing company) conducting a formal review and improvement of their quality management system. However, the narrative suggests that the company, under the leadership of Efraim Diveroli and David Packouz, is primarily motivated by profit and securing lucrative arms deals rather than emphasising a robust quality management system. The film highlights instances where AEY cuts corners to maximise profits, leading to questionable practices and ethical dilemmas. Consequently, the storyline emphasises the consequences of prioritising financial gains over ethical and quality considerations in the context of international arms dealing.
- Moneyball (Oakland A's): Billy Beane built a successful team without a traditional business plan; instead, he made decisions as he went along and eventually stumbled upon Peter Brand, who believed in the predictive analytics system. This approach led the Oakland A's to a 20-game winning streak, breaking records in American baseball history.
- Explore further insights on How to implement systems and procedures derived from our case study movies: The Founder, War Dogs and Moneyball by clicking here.
CONTEXT
Management control, systems, and procedures hold managers accountable for an organisations performance. System and procedures ensure that entrepreneurs and business managers meet customers expectations and improve the brand of the business, both of which are critical to the growth of a healthy business. Management control, system, and procedure are all management functions that aid in the detection of errors and the implementation of corrective actions. This is done to reduce deviation from standards and ensure that the organisations stated goals are met in the desired manner. This skills programme provides a platform and tools for entrepreneurs and business managers to create business systems and procedures in minutes.
Description
Examine and improve in detail how audit results are handled.
Purpose
Be able to see a connection between phenomena, context, and people. To provide capability to capture the context and lived reality of participants.
Rational
Effective record-keeping and monitoring are critical to the QMSs success, ability to obtain maintain clean operation, and regulatory compliance.
Key Lessons
Click here and draft your business plan in minutes
To request tailored accredited training and enterprise development services, contact us at businessplan@superdealmaker.com.
Get List for Funding Opportunities in Minutes, Click Here
To request tailored investment banking services, contact us at businessplan@superdealmaker.com.
QMS Evaluation and Enhancement: Contrasting AEY's Misstep with McDonald's and A's Triumphs
AEY's Oversight: A Quality Quagmire
AEY, in the turbulent world of arms dealing, serves as a stark example of quality mismanagement. Their failure to review and enhance their quality management system (QMS) created fissures that led to the infiltration of substandard products into their supply chain. Compliance woes and tarnished credibility ensued, emphasising the dire consequences of neglecting the critical aspect of quality control.
McDonald's Triumph: Golden Arches of Quality
In stark contrast, the saga of McDonald's unveils a tale of meticulous quality management. Ray Kroc and team recognised the essence of consistently delivering a superior customer experience. Their commitment to the Speedee Service System and rigorous quality standards not only ensured customer satisfaction but also laid the foundation for global fast-food dominance. The Golden Arches, synonymous with quality, became an enduring symbol of success.
A's Strategic Brilliance: Quality at the Core
Shifting gears to the baseball diamond, the story of Moneyball and the Oakland Athletics underscores the importance of strategic brilliance in quality. Billy Beane and Peter Brand revolutionised player selection, emphasising statistical analysis. This data-driven approach wasn't just about winning games; it was about enhancing the quality of player performance. The A's success wasn't a stroke of luck; it was a testament to leveraging insights for continuous improvement.
Lessons Learned: Quality as the Cornerstone
The tales of AEY, McDonald's, and the A's offer a profound lesson in the world of business. Quality management is not a mere checkbox; it's the cornerstone of enduring success. Entrepreneurs, take heed: in the pursuit of your ventures, let the contrasting stories guide your path. Fortify your quality management systems, embrace innovation, and ensure that excellence becomes the heartbeat of your journey.
Enhancing SME Efficiency: Review and Improve Quality Management System
A quality management system (QMS) is a set of processes, policies, and procedures that an organisation implements to ensure that its products or services consistently meet customer requirements and comply with applicable regulations. Regular review and continuous improvement of the QMS are essential to enhance its effectiveness and optimise organisational performance.
The management review process requires Top Management to review the Quality Management System on a regular basis to ensure its continued suitability, adequacy, and effectiveness, while also addressing the possibility of changes to quality policy, objectives, targets, and other elements of the QMS.
Top Management, functional managers, facility managers, line managers, process owners, process users, and action owners should all be represented in the management review.
The management review's goal and final outcome should be continuous improvement of the QMS and quality manuals. As your organisation's QMS improves in terms of effectiveness and efficiency (via corrective and preventive actions and audit findings), so will the performance and improvement process.
Aim to conduct a management review at least once a year, or more frequently if necessary. Little and often is best; there's no reason to go through the entire agenda each time, and there's no reason to duplicate effort if you cover certain aspects as part of other management meetings.
Management reviews could occur quarterly, six months, or annually. Management reviews can be conducted independently or in conjunction with other business activities such as strategic planning, business planning, operations meetings, process reviews/councils, customer requirements, or functional reviews.
The format, frequency, and intervals of management review meetings are determined by your organisation, but they must be specified in the QMS.
Review Process
- Evaluation of Objectives: Assess the achievement of established quality objectives and determine if they are aligned with the organisation's overall goals.
- Data Analysis: Collect and analyze relevant data, including customer feedback, quality metrics, and performance indicators, to identify areas for improvement.
- Audit and Compliance: Conduct internal and external audits to ensure compliance with quality standards and regulatory requirements.
- Management Review: Hold regular management reviews to evaluate the effectiveness of the QMS, identify opportunities for improvement, and allocate necessary resources.
Improvement Process
- Corrective Actions: Take corrective actions to address identified non-conformities, eliminate root causes, and prevent recurrence of quality issues.
- Preventive Actions: Implement preventive measures to proactively identify and mitigate potential quality problems before they occur.
- Continuous Training: Provide ongoing training and development opportunities to enhance employees' knowledge and skills related to quality management.
- Process Optimisation: Streamline processes, eliminate unnecessary steps, and improve efficiency to enhance overall quality and reduce waste.
By regularly reviewing and improving the QMS, organisations can ensure that their products or services consistently meet or exceed customer expectations, drive customer satisfaction, and maintain a competitive edge in the market.
It is not required to document the management review process; however, we believe it is beneficial to the business and recommend that you develop and implement a Management Review Procedure that defines:
- Management review responsibilities - at what level of management, senior manager, facility manager etc.
- Management review scheduling
- Management review inputs (agenda)
- Management review outputs (minutes, actions)
When to Review and Improve Quality Management System
A quality management system (QMS) should be reviewed and improved on a regular basis to ensure its continued effectiveness and alignment with organisational goals. The following are key points to consider:
- Periodic Reviews: Conduct scheduled reviews of the QMS at predefined intervals. This could be annually, biannually, or as determined by the organisation's quality objectives and requirements.
- Trigger Events: Initiate a review of the QMS when significant changes occur within the organisation, such as mergers, acquisitions, changes in regulations, or shifts in customer needs and expectations.
- Customer Feedback: Monitor and analyze customer feedback to identify areas for improvement and address any recurring issues or concerns.
- Process Performance: Continuously monitor key performance indicators (KPIs) and quality metrics to evaluate the performance of processes within the QMS. If there are deviations or trends indicating a decline in performance, it may be time to review and improve the system.
- Internal and External Audits: Conduct regular internal audits to assess compliance with quality standards and regulatory requirements. External audits by certification bodies or regulatory agencies may also prompt the need for reviewing and improving the QMS.
- Management Review Meetings: Hold periodic management review meetings to evaluate the effectiveness of the QMS, identify areas for improvement, and set improvement objectives.
By reviewing and improving the QMS at appropriate intervals and in response to relevant triggers, organisations can ensure that their quality management processes remain effective, efficient, and aligned with their strategic objectives.
What Should Be Reviewed?
Customer feedback, audit findings and audit results (using a gap analysis tool or internal audit checklist), and internal and external issues should be discussed by the management team; process performance, quality objectives, preventive actions, and recommendations for improvement - and their potential impact on the organisation's strategic direction.
Management review meetings must address the potential need for changes to policy, objectives, targets, and other quality management system elements (QMS). The management review process must ensure that all necessary information is gathered ahead of time to allow management to carry out this evaluation effectively.
Internal Review Factors
- Minutes from previous management reviews
- The policies, objectives and targets
- Results of QMS and process audits
- The extent to which objectives and the numeric targets were met
- Assessment of risk management actions
External Review Factors
- New or proposed legislation or regulations
- External providers and suppliers performance
- Changing expectations/requirements of relevant interested parties (customer feedback, customer requirements)
- New or modified activities, products, or services
- Advances in technology and science
- Changing market preferences of buyers
The management review's purpose and final outcome should be continuous improvement of the quality system (QMS) using recommendations for improvement. As the effectiveness and efficiency of your organisation's quality management systems improve, so will its environmental management
The management review's purpose and final outcome should be continuous improvement of the quality system (QMS) using recommendations for improvement. As the effectiveness and efficiency of your organisation's quality management systems improve, so will its environmental management
Passion for Perfection: Ray's Pursuit of Excellence at McDonald's
In the bustling world of fast food, Ray Kroc's commitment to excellence went beyond speedy service. Recognising that quality was the heartbeat of customer satisfaction, Ray initiated a profound review and enhancement of McDonald's Quality Management System. Picture this as the turning point where the Golden Arches shifted from merely serving food to crafting an experience steeped in quality and consistency.
Ray's meticulous review of the Quality Management System had a seismic impact on McDonald's. It wasn't just about ensuring that every burger and fry met a certain standard; it was about creating an unwavering trust with customers. The enhanced system not only elevated the taste and consistency of the food but also streamlined operations, reducing errors and waste. In the competitive landscape of fast food, quality became McDonald's secret sauce for enduring success.
Ray's approach to enhancing the Quality Management System was more than a theoretical overhaul—it was a practical revolution. He implemented rigorous training programs, ensuring that every staff member understood the importance of quality in their role. Regular inspections, feedback loops, and supplier partnerships were established to create a seamless quality chain. The impact wasn't just on the taste of the Big Mac; it was on the brand's reputation and the trust it instilled in customers worldwide.
Ray's passion for perfection echoes in every bite under the Golden Arches. The legacy he carved out through the review and enhancement of McDonald's Quality Management System is a testament to the enduring value of uncompromising quality in business. Entrepreneurs, take note: in the pursuit of excellence, the impact is not just on the product but on the customer experience and the longevity of your brand.
Billy Beane's Quality Revolution at the Oakland A's
Enter the world of baseball, where Billy Beane, the maverick general manager of the Oakland Athletics, orchestrated a quality management revolution. Recognising the need for a more data-driven approach, Billy embarked on a mission to review and enhance the team's quality management system. It wasn't just about wins and losses; it was about redefining the game through a lens of statistical precision.
Billy's commitment to quality extended beyond the field, seeping into the core of decision-making. The traditional scouting system was overhauled as statistical analysis took center stage. By embracing advanced metrics and scrutinising player performance data, the A's aimed not just for victories but for a strategic advantage. The impact was profound—transforming the way baseball teams approached talent evaluation and team building.
The review and improvement of the quality management system were driven by a desire to break free from convention. Billy recognised that the key to success lay in embracing innovation and challenging the status quo. By prioritising data-backed decisions, the A's aimed to minimise uncertainties in player performance assessment and, consequently, enhance the overall quality of their team.
Billy Beane's journey offers entrepreneurs valuable lessons. Quality management isn't confined to manufacturing; it extends to strategic decision-making. By leveraging data and embracing innovation, businesses can redefine their industries. So, entrepreneurs, take a swing at quality management, and who knows—you might hit a home run in your industry!
How to Review and Improve SME Processes: System and Procedures for QMS Enhancement
A Management Review, like any other successful meeting, should be planned ahead of time. You must decide when it will be held, what will be discussed, and who should attend. ISO Standards require you to document when meetings should take place and what will and has been discussed, but it is also a good idea to keep a list of attendees.
Set Management Review Agenda
To allow management to perform the review effectively, the management review process must ensure that all necessary information is gathered ahead of time (an audit checklist can help here).
A successful management review process should prioritise the following inputs:
- Risks and opportunities
- Possible changes that might affect the system
- External provider and suppliers performance
- Customer satisfaction and perception
- Audit results
- Nonconformity and corrective actions
Set a Schedule
A meeting should be held at least once a year, but meetings can be held quarterly or even monthly if preferred.
Joint Management Reviews may be conducted to save time and avoid unnecessary duplication if your organisation operates more than one Management System or has a Management System that is certified to more than one ISO Standard. Make sure you cover both the unique aspects of each Standard and the shared features.
It is possible for businesses that hold multiple meetings throughout the year to dedicate each meeting to the review of a specific section or area of your Management System. If you to conduct multiple reviews in this manner, ensure that the reviews cover all of the topics required by the ISO Standard to which you are certified. This is made easier by creating a detailed agenda for each meeting.
Write an Agenda
Producing an agenda for your meeting is an important part of your planning; it is also a requirement for ISO Certification, so it is good practice to do so. A detailed and agreed-upon agenda will assist you in ensuring that all topics required by your chosen ISO Standard are covered, especially if you decide to hold multiple reviews throughout the year on different topics.
The following topics should be covered in a Management Review:
- Discussion of any outstanding issues from the previous meeting.
- External and internal changes that have an impact on the Management System
- Examination of the Management System's performance
- Examine the available resources and their sufficiency
- Examine how effective the actions taken in response to identified risks and opportunities were.
- Identifying additional opportunities for improvement
Document the Attendees
Once you've established an agenda, you can ensure that the appropriate people are present to discuss the issues.
The meeting should be chaired by the person with overall responsibility for the Management System, and it is their responsibility to designate senior management members who must attend and actively participate in Management Review.
In general, the senior management team should attend a Management Review, but others may be invited to discuss specific issues that require more detail.
Management Review Outputs (Minutes/Actions)
Management reviews must be documented at all times. The review's observations, conclusions, and recommendations for further action must be documented. If corrective action is required, Top Management should monitor its implementation to ensure that it is effective.
Auditors should expect to see the same results from management reviews; however, they should be aware that management review results can now be stored in any format that the organisation chooses.
Typical outputs might include:
- Process improvement actions (including preventive actions)
- QMS improvement actions
- Product improvement actions
- Resource provision actions
- Revised business plans and budgets
- Changes to quality objectives and policies
- Management meeting minutes
Take Minutes
Because ISO Certification requires you to document the content and outcomes of your Management Review meetings, someone will need to take minutes throughout the meeting.
When taking minutes, refer to the meeting agenda and make notes next to each related topic. This will aid in the subsequent write-up because brief notes have more context when written under specific topics.
You should detail who is responsible for the task and the assigned deadline for any agreed-upon actions or changes that must be carried out. These items can be more easily followed up on in subsequent Management Reviews if this information is recorded.
Make a note of the meeting's date and time, as well as who was present.
It is critical to write the minutes as soon as possible after the meeting to ensure the contents are fresh in your mind. This is because the ISO Standard requires the minutes to be documented and made available to third-party auditors.
Minutes of management review meetings should be kept as documentation for the quality management system.
The following are the minutes of the management review meeting:
- Action items are highlighted to make them easily identifiable.
- The assignment of responsibility is one of the action items.
- Action items include a timetable and resource allocation for implementation.
Auditors will look for evidence of the same types of output from management reviews as they did in the previous version of the standard. However, keep in mind that the results of management reviews can now be kept in any format your organisation prefers. Businesses are now required to keep documented information as proof of the outcomes of management reviews.
Measuring Management Review Effectiveness
The effectiveness of key decisions/outputs, such as budgetary changes, forecasts, revised resource plans, or changes to the quality policy or objectives, can be measured as part of the management review process. Management review outputs are intended to improve your business; for international standards, certification body auditors will look for evidence that this is being achieved.
The use of fact-based decision making, which is the use of figures and evidence to evaluate the outcome of a proposed decision before implementing it, is an important aspect of ISO Certification. Examining appropriate evidence is critical to this process because a Management Review meeting involves making decisions about changes to and the direction of company policies and the Management System.
The following evidence should be brought to a Management Review:
- Minutes of previous Management Review meeting
- Management System documentation
- Internal and External Audit Reports
- Relevant records (including customer feedback, corrective action log etc.)
- Register of Legal and other requirements
- Complaints analysis
- Corrective and preventive actions and close-out of Management Information Reports
- Policies review
Look at Trends
To keep your Management System improving, you must look for trends both inside and outside of your company. Trends can point to recurring issues that, while they can be resolved individually when they occur, can be completely avoided by implementing broader changes to business processes. They can also identify potential issues that, while not affecting your business right now, may have far-reaching consequences in the future.
Consider looking for trends in the following areas:
- External interested parties' requirements
- Compliance with laws, regulations, and other requirements
- Product, service, and process changes
- Records of customer satisfaction and complaints
- Nonconformities and the efficacy of any corrective actions taken in response
After the Review
The minutes, or portions thereof, should be distributed to all appropriate members of staff. This is especially important if any of the meeting's discussions include decisions and actions concerning:
- Are there any areas of the business that could be improved?
- Any required changes to the Management System, processes, or policies Any revisions to company objectives or Key Performance Indicators (KPIs)
- Any changes to business plans or budgets
- Any changes to the resources required for the Management System to run smoothly
These types of changes have an impact on day-to-day operations, so it is critical to keep staff informed of these changes to ensure that your Management System is functioning properly.
Ineffective System and Procedures: AEY's Oversight and Its Impact
In the high-stakes world of arms dealing, AEY, driven by the allure of lucrative government contracts, found themselves entangled in a web of oversight failure, particularly in their quality management system. The critical task of systematically reviewing and enhancing their processes took a backseat, opening the door to a host of issues. This neglect allowed discrepancies and inefficiencies to proliferate within their operations, setting the stage for a critical breakdown in their quality management.
The repercussions of AEY's failure to uphold a robust quality management system were profound. Substandard products, resulting from lax oversight, were delivered to clients, eroding trust and damaging the company's hard-earned reputation. The ripple effect extended to legal ramifications, with contracts being terminated and legal battles ensuing. The financial toll was significant, and AEY found themselves in the crosshairs of regulatory scrutiny, facing fines and penalties for their negligence.
AEY's quality management fiasco serves as a cautionary tale for entrepreneurs. It underscores the paramount importance of prioritising and continually improving quality control processes. Entrepreneurs must establish a robust system for regular reviews, identifying areas for enhancement to ensure products or services not only meet but exceed expectations. Neglecting this vital aspect can lead to a domino effect of consequences that are not only financial but also tarnish the reputation and integrity of the business. Aspiring business leaders, take heed: proactive quality management is the bedrock of sustainable success.
System Optimisation for SMEs: QMS Evaluation and Enhancement
Ensuring a robust quality management system (QMS) is not just a regulatory necessity but a strategic imperative for businesses. Regular and thorough reviews of the QMS form the cornerstone of improvement efforts. Through systematic audits and feedback collection from stakeholders, including customers and employees, businesses can pinpoint areas that need enhancement. This critical analysis enables organisations to stay aligned with industry standards, mitigate risks, and maintain a competitive edge.
However, the journey towards excellence doesn't end with reviews—it extends into a culture of continuous improvement. Businesses must integrate feedback mechanisms and KPIs to monitor the effectiveness of their QMS. Employee training programs play a pivotal role, fostering a workforce that is not only compliant with quality standards but actively contributes to ongoing improvement initiatives. This commitment to perpetual enhancement positions businesses to adapt to changing market demands, enhance customer satisfaction, and fortify their reputation for delivering quality products or services.
In essence, a dynamic and responsive QMS is a linchpin for organisational success. Beyond mere compliance, it becomes a strategic asset that propels businesses towards excellence. By institutionalising a commitment to quality at every level and constantly refining processes, businesses can build resilience, foster innovation, and cultivate enduring customer trust.
Join the Conversation: Share Your Thoughts on This Article
- No comments yet.
Add Your Comment Now!