Implementing Corrective and Preventative Actions for SME Quality Management
Discover effective strategies to enhance your SME's quality management systems with corrective and preventative actions. Learn practical methods to optimize procedures and ensure sustained operational excellence.
Optimise your business operations with a proactive approach to issue resolution and prevention. Our guide emphasises the importance of robust systems for identifying and addressing challenges. Learn how to conduct effective root cause analyses, develop targeted corrective action plans, and establish preventative measures to enhance operational efficiency.
|
Essential Guide: Implementing Corrective and Preventive Actions for SMEs
Understanding how to implement corrective and preventive actions (CAPA) is vital for the success of small and medium enterprises (SMEs). Proactive identification and resolution of issues can prevent costly mistakes, enhance efficiency, and maintain customer satisfaction. This comprehensive guide explores the importance of CAPA for SMEs, providing actionable strategies to address problems at their root cause and prevent recurrence. Learn how to streamline processes, mitigate risks, and foster continuous improvement to ensure the long-term success and resilience of your SME. With effective CAPA implementation, SMEs can optimise operations, build credibility, and thrive in competitive markets.
Implementation of Corrective and Preventative Actions Considerations
- Implementing corrective and preventative actions is crucial for businesses to maintain operational efficiency and improve overall performance. Firstly, businesses should establish a robust system for identifying and addressing issues. This involves conducting thorough root cause analyses to understand the underlying factors contributing to problems. Once issues are identified, businesses should develop corrective action plans that are targeted and specific, addressing the root causes rather than just the symptoms. These plans should include clear responsibilities, timelines, and measurable objectives to track progress. Regular monitoring and feedback loops are essential to ensure that corrective actions are implemented effectively and that any deviations from the plan are promptly addressed.
- Secondly, a proactive approach to preventative actions is essential to minimise the occurrence of issues in the first place. This involves continuous risk assessment and anticipation of potential challenges. Businesses should implement preventative measures, such as robust quality control processes, employee training programs, and regular equipment maintenance, to reduce the likelihood of problems arising. Additionally, fostering a culture of continuous improvement and learning within the organisation encourages employees to identify and address potential issues before they escalate. Establishing key performance indicators (KPIs) and metrics for monitoring processes can help in identifying early warning signs, allowing businesses to take preventative actions proactively. By integrating both corrective and preventative actions into their management systems, businesses can enhance their resilience and long-term sustainability.
- Exaggeration Impact: Some movies incorporate exaggeration as a storytelling or artistic technique. This exaggeration can involve elements like larger-than-life characters, over-the-top action sequences, or surreal visual effects. While these exaggerations can enhance the cinematic experience, they might lead to misinterpretations or overlooking the subtler aspects of the film.
How to implement corrective and preventative actions
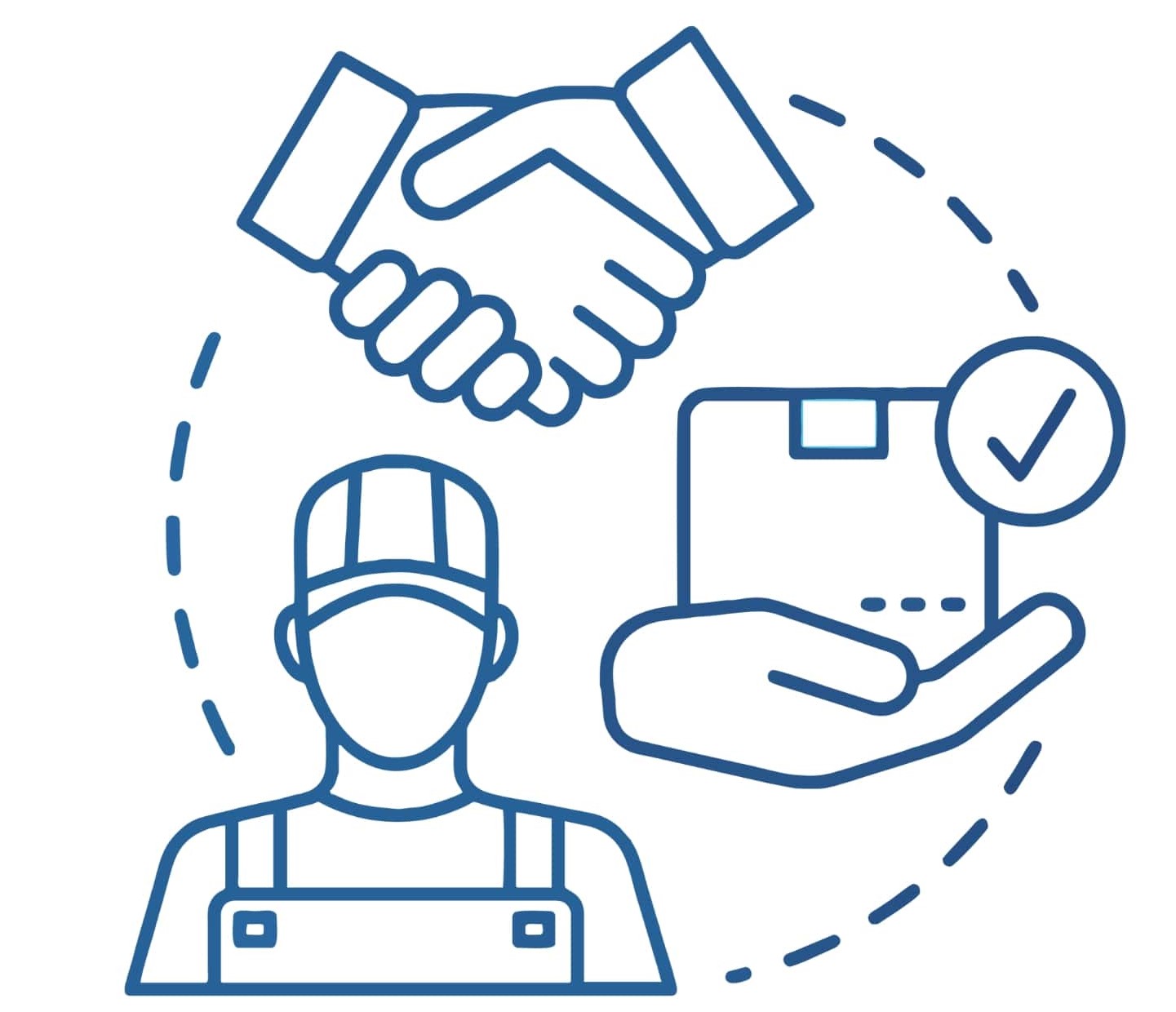
Written by: Malose Makgeta
MBA with 20+ years experience in SME development and funding. LinkedIn Profile
Implementation of Corrective Actions - Entrepreneurship Lessons from Movies The Founder, War Dogs and Moneyball
- The Founder (McDonald's): The first restaurant opened by the McDonald brothers was not initially successful, leading them to redesign it into what we now recognise as McDonald's. Ray Kroc, who joined later, hadn't perfected the initial business model, nor did he have a detailed business plan. Both the McDonald brothers and Ray faced near failure because they lacked a business plan. Fortunately, they had the resources to delve deep into the business without one. If you have the resources, you can start without a business plan; otherwise, a business plan is critical.
- War Dogs (AEY): AEY implemented corrective and preventative actions in response to challenges and risks associated with their arms dealing business. As issues arose, such as logistical problems and legal complications, the company took corrective measures to address immediate concerns. This involved resolving operational inefficiencies, handling legal disputes, and ensuring the timely delivery of contracted goods. Simultaneously, AEY demonstrated a commitment to preventative actions by instituting more robust internal controls, compliance measures, and risk mitigation strategies to avoid future pitfalls. These actions aimed to enhance the company's overall performance, compliance with regulations, and reputation within the international arms industry.
- Moneyball (Oakland A's): Billy Beane built a successful team without a traditional business plan; instead, he made decisions as he went along and eventually stumbled upon Peter Brand, who believed in the predictive analytics system. This approach led the Oakland A's to a 20-game winning streak, breaking records in American baseball history.
- Explore further insights on How to implement systems and procedures derived from our case study movies: The Founder, War Dogs and Moneyball by clicking here.
CONTEXT
Management control, systems, and procedures hold managers accountable for an organisations performance. System and procedures ensure that entrepreneurs and business managers meet customers expectations and improve the brand of the business, both of which are critical to the growth of a healthy business. Management control, system, and procedure are all management functions that aid in the detection of errors and the implementation of corrective actions. This is done to reduce deviation from standards and ensure that the organisations stated goals are met in the desired manner. This skills programme provides a platform and tools for entrepreneurs and business managers to create business systems and procedures in minutes.
Description
How to implement corrective and preventative actions quality system consists of the specific improvements an organisation makes to its processes to eliminate non-conformities.
Purpose
Be able to record non-conformances and corrective actions resolved according to organisational requirements.
Rational
Control must be revised to ensure that any changes to quality management systems are properly approved and evaluated for any potential impact on the business.
Key Lessons
Click here and draft your business plan in minutes
To request tailored accredited training and enterprise development services, contact us at businessplan@superdealmaker.com.
Get List for Funding Opportunities in Minutes, Click Here
To request tailored investment banking services, contact us at businessplan@superdealmaker.com.
Contrasting Corrective and Preventative Actions: McDonald's, Moneyball, and War Dogs
McDonald's: Systematic Standardisation and Innovation
McDonald's, with its emphasis on systematic standardisation, implemented corrective and preventative actions by fine-tuning its operations. The introduction of the Speedee Service System showcased a commitment to efficiency and consistency. Preventative actions were evident in the franchise model, where standard operating procedures served as a buffer against potential deviations. Innovations, such as the introduction of new menu items and marketing strategies, represented corrective actions to adapt to changing consumer preferences.
Moneyball: Data-Driven Player Selection and Market Exploitation
In the realm of baseball, Moneyball's corrective and preventative actions were rooted in a data-driven approach. Billy Beane's focus on undervalued players and market inefficiencies served as both a corrective action, challenging traditional scouting methods, and a preventative action against overreliance on conventional wisdom. The use of data analytics allowed the Oakland Athletics to proactively identify potential pitfalls in player selection and exploit opportunities in the market.
War Dogs: Ethical Considerations and Risk Mitigation
War Dogs, operating in the complex world of government contracting, implemented corrective and preventative actions with a focus on ethics and risk management. Ephraim and David navigated ethical dilemmas as a corrective measure to ensure the legality and sustainability of their ventures. In terms of risk mitigation, their actions involved careful consideration of potential legal consequences, actively preventing issues that could arise from engaging in illicit arms deals. War Dogs' approach showcased the importance of ethical considerations and proactive risk management in their industry.
Implementing Systems for SMEs: Preventive vs Corrective Measures
Preventive action is taken to address the root cause of a process problem before it occurs. A preventive action (PA) definition in a management system could be: "the activities undertaken by the organisation to eliminate the cause of a potential process nonconformity." Preventive action is defined as identifying potential problems that could occur in a process, assessing what could cause these problems, and taking action to prevent the problem from occurring before it occurs.
Corrective action (CA) refers to the steps taken to eliminate the source of a process nonconformity. Corrective action is the activity of responding to a process problem, bringing it under control through containment actions, and then taking the necessary action to prevent it from happening again.
Preventive actions identify the problem before it occurs and take steps to fix the cause of the problem before it happens, as opposed to corrective actions, which act to address the cause of a problem after it has already occurred. An easy corrective action and preventive action (CAPA) example is provided below:
- Corrective action: After injuring myself on a table's corner and realising that the table's sharp corners were to blame, I took steps to have the table's corners rounded off to prevent any further injuries. This includes the steps taken to modify the design so that rounded corners are used in all future tables.
- Preventive action: I discover that a table's sharp corners are to blame for the risk of someone being cut (despite the fact that no one has been hurt), so I round the corners and modify future designs to eliminate the risk.
While corrective action and preventive action in the management system typically involves process issues, this example uses a product issue instead, making it simple to understand the distinction between preventive actions and corrective actions. In other words, corrective measures are taken in response to problems after they occur, whereas preventive measures are taken in advance of potential problems.
As part of the management system, there are corrective action and preventive action processes. Both processes essentially followed the same steps, but corrective action was initiated in response to an actual problem, whereas preventive action was started in response to the identification of a potential problem. When implementing earlier versions of these management systems, there was frequently confusion about this; some people only occasionally used their preventive action process because it is a complicated process and diverts time from reacting through corrective actions. Others considered any steps taken as part of the corrective action process to stop a recurrence to be preventive actions.
International organisation for Standardisation ("ISO") - According to ISO, the complicated procedure that was formerly associated with PA is unnecessary and that other provisions of the standard can actually deliver effective good preventive actions when used properly. Now, other provisions of the standard have taken the place of preventive action, including:
- Risk-based thinking – This new requirement asks you to identify potential management system-impacting areas where the results are uncertain. This way of thinking involves recognising this uncertainty, or risk, and deciding whether you need to take action to avoid negative outcomes or to take advantage of positive outcomes; these are risks and opportunities (essentially positive risk).
- Improvement - Any actions you take to improve your management system's processes are considered preventive measures. The new requirements place less emphasis on having the intricate preventive action system in place from previous versions of the standards and more emphasis on each company finding good ways that work for them to improve processes. This could be a step to avoid a problem if you have something as simple as a suggestion program that finds ways to improve processes and puts those changes into practice.
Ensuring Success: SMEs and Preventive Action Strategies
Preventative measures is to ensure the prevention of systems and procedures failure, it is crucial to implement a set of preventative measures. First, regular system backups should be conducted to safeguard against data loss. Additionally, comprehensive testing and debugging should be performed during the development phase to identify and rectify potential issues. Strong access controls and security protocols should be put in place to protect against unauthorized access and data breaches. Regular monitoring and maintenance should be carried out to detect and address any system vulnerabilities or performance issues. Lastly, thorough documentation of procedures and guidelines should be maintained to ensure consistency and facilitate troubleshooting. By following these preventative measures, the risk of systems and procedures failure can be minimised, promoting a stable and reliable operational environment.
1. Security Measures
- Implement strong passwords and regular password updates for all business accounts.
- Use two-factor authentication for sensitive systems and applications.
- Regularly update and patch software and systems to address security vulnerabilities.
- Install and update anti-malware and firewall software on all devices.
- Restrict access to sensitive data and systems based on job roles and responsibilities.
- Train employees on safe browsing habits and how to identify and report potential security threats.
2. Data Protection Measures
- Implement data encryption for sensitive information stored on servers, databases, and portable devices.
- Establish regular data backup procedures and store backups in secure off-site locations.
- Develop and enforce a clear data retention policy to ensure compliance with legal and regulatory requirements.
- Regularly review and update privacy policies to reflect any changes in data handling practices.
- Limit access to confidential data on a need-to-know basis and monitor access logs regularly.
3. Workplace Safety Measures
- Conduct regular safety inspections and address any hazards or potential risks.
- Provide appropriate safety equipment and training to employees for their specific roles.
- Establish and communicate emergency procedures, including evacuation plans and assembly points.
- Maintain a clean and organised work environment to prevent accidents and injuries.
- Promote a culture of safety by encouraging employees to report any safety concerns or incidents.
4. Compliance Measures
- Stay updated on relevant laws, regulations, and industry standards applicable to the business.
- Develop and implement policies and procedures to ensure compliance with legal and regulatory requirements.
- Regularly review and update policies and procedures to align with any changes in laws or regulations.
- Provide training to employees on compliance-related topics, including anti-corruption and anti-discrimination policies.
- Establish mechanisms for reporting and investigating potential compliance violations.
McDonald's Recipe for Corrective and Preventative Actions
Ray Kroc, the visionary behind McDonald's, understood the inevitability of business missteps. When challenges arose, Ray didn't shy away; instead, he embraced corrective actions with strategic acumen. Whether it was addressing operational inefficiencies or refining the customer experience, Ray's keen eye for identifying weaknesses paved the way for continuous improvement.
Ray Kroc's business philosophy extended beyond merely addressing issues as they arose. He was a proponent of preventative actions—strategies designed to anticipate and avert potential challenges. By implementing stringent quality control measures, standardized processes, and ongoing training programs, Ray aimed to create an environment where issues were not just fixed but anticipated and prevented.
The impact of Ray's meticulous approach to corrective and preventative actions was profound. McDonald's, under his guidance, became synonymous with efficiency, consistency, and customer satisfaction. By addressing issues head-on and proactively implementing preventative measures, McDonald's not only weathered storms but emerged as an industry leader. The commitment to continuous improvement, a hallmark of Ray's legacy, is a valuable lesson for businesses navigating the ever-evolving landscape.
How SMEs could Implement Preventative Action
- Clear Documentation: Develop comprehensive and well-documented policies and procedures that are easily accessible to all employees.
- Documented Findings: Document the findings from the analysis to have a clear understanding of the issues at hand.
- Regular Review and Updates: Conduct periodic reviews of policies and procedures to ensure they remain relevant and effective.
- Effective Communication: Establish clear communication channels to disseminate policies and procedures throughout the organisation.
- Consistent Enforcement: Ensure consistent enforcement of policies and procedures across all levels of the organisation.
- Risk Assessment: Conduct regular risk assessments to identify potential areas of failure and develop preventive measures to mitigate those risks.
- External Expertise: Seek external expertise or consult industry best practices to enhance the effectiveness of policies and procedures.
- Management Support: Obtain buy-in and support from top management to ensure policies and procedures are prioritised and allocated the necessary resources.
- Thorough Analysis: Conduct a detailed analysis to identify the root causes of the policy or procedure failure.
- Collaborative Approach: Involve relevant stakeholders in the decision-making process for implementing corrective measures.
- Revision and Improvement: Revise the existing policies and procedures to address identified deficiencies and improve their effectiveness.
- Employee Training: Provide thorough training on policies and procedures to ensure employees understand their responsibilities and how to follow the guidelines.
- Training and Education: Provide training sessions and educational resources to employees to enhance their understanding and compliance with the revised policies and procedures.
- Communication and Awareness: Implement a communication plan to ensure all employees are aware of the changes made to the policies and procedures.
- Monitoring and Evaluation: Establish mechanisms to monitor and evaluate the implementation and effectiveness of the corrective measures.
- Feedback Mechanisms: Create channels for employees to provide feedback, suggestions, and report any concerns regarding the policies and procedures.
- Continuous Improvement: Foster a culture of continuous improvement by regularly reviewing and updating policies and procedures based on feedback and changing business needs.
- Accountability and Enforcement: Clearly define roles and responsibilities for policy enforcement and ensure consistent accountability across the organisation.
Preventive Action Plan
A preventive action plan, developed for preventive actions, must include all of the elements outlined above for a corrective action plan. If you are taking action to eliminate an identified risk, you should treat it as a project, with the same level of oversight and resource budgeting. It is important to note, however, that even a CA plan includes elements to prevent the problem from recurring in the future. The PA plan differs in that it is implemented proactively for a potential problem rather than in response to an existing problem.
AIt makes perfect sense to encourage your top management team to embrace changes in leadership requirements and to pair this with a new risk-based thinking process. The sooner you can facilitate both and encourage their synergy, the more sensitive your organisation will be to the threats and risks it will face in the coming months and years. And, as we all know, where there are risks, there are almost always opportunities, so identifying these is another advantage of implementing this overall strategy as soon as possible. Risk elimination and mitigation almost always ensures company growth, which can only be good for your organisation.
When dealing with a systemic problem, one that is not caused by a one-time error but rather by something in the system, ignoring it can cost you a lot of time and money. That is why corrective action is critical. If people are performing unnecessary activities to constantly fix problems that occur, or if they must be constantly vigilant to catch problems that occur all the time before they escalate, you can save a lot of resources by taking the necessary actions to prevent the problems from occurring again. To save you time and money, the CA process is part of the Quality Management System.
It is important to note that one of the problems with the corrective action process is that it is difficult to use for small, non-systemic problems where a root cause cannot be identified. Once the discovered problem has been resolved, you can assess the need to take action to eliminate the root cause of the nonconformity. If you determine that this isn't necessary, such as for a one-time problem that shows no signs of recurring, you can halt the corrective action process. You should still follow up to ensure that the problem does not reoccur, and if it does, you should reconsider your decision and take additional steps.
Corrective action entails more than just fixing a minor issue; it entails addressing a systemic issue that requires elimination rather than a minor error that requires correction. When a systemic problem is discovered, a leader must take corrective action. Here are some examples of things leaders should look at to identify potential systemic issues:
- Key performance indicators (KPI) - Do the performance indicators you've chosen indicate any routine issues? Do your KPIs show that your processes are running smoothly?
- Review of records - Do your records reveal recurring issues that should be investigated, such as a cyclic delay that occurs on a specific date each month?
- Employee feedback - Do you need to investigate further if employees suggest issues that they are constantly resolving?
- Audit findings - Audits are used to identify areas where processes are not meeting planned requirements, and assessing these flaws may reveal systemic issues. Internal audits, customer audits, and certification audits are all included.
When to Take Preventative Measures
- During Policy Development: Incorporate preventative measures from the outset when creating new business policies and procedures.
- When Implementing Changes: Prioritise preventative measures when introducing modifications or updates to existing policies and procedures.
- Periodic Reviews: Conduct regular reviews of policies and procedures to identify areas of weakness or potential failure.
- After Incidents or Failures: Take preventative measures after incidents or failures occur to prevent their recurrence.
- When Identifying Risks: Implement preventative measures when assessing risks associated with specific policies and procedures.
- Upon New Regulatory Requirements: Stay proactive and adapt policies and procedures to meet new regulatory standards.
- When Expanding or Restructuring: Evaluate and update policies and procedures to accommodate changes during business expansion or restructuring.
- Employee Onboarding: Include preventative measures as part of the onboarding process to ensure new employees are aware of and follow established policies and procedures.
- After Feedback or Suggestions: Consider preventative measures based on employee feedback, suggestions, or identified areas for improvement.
- As Part of Continuous Improvement: Integrate preventative measures into the ongoing process of enhancing policies and procedures through continuous improvement initiatives.
Billy Beane's Playbook: Corrective and Preventative Actions at the A's
Enter Billy Beane, the mastermind behind the Oakland Athletics' revolutionary approach to baseball. In the quest for success, Billy recognised the need for corrective and preventative actions to reshape the team's destiny. His strategic moves went beyond mere player selection; they were a paradigm shift in how baseball teams operated. Billy, acknowledging the limitations of traditional scouting, harnessed the power of data and analytics to identify undervalued players and exploit market inefficiencies.
Billy Beane's implementation of corrective and preventative actions was nothing short of revolutionary. He actively sought players undervalued by traditional metrics, identifying market inefficiencies that became the team's competitive advantage. This proactive strategy was a corrective action, addressing the flaws in conventional player assessment methods. Moreover, by investing in players with skills often overlooked, Billy prevented potential pitfalls that could arise from relying solely on conventional wisdom.
The impact of Billy Beane's corrective and preventative actions was monumental. The A's went on an unprecedented winning streak, showcasing the efficacy of data-driven decision-making in baseball. Billy's legacy extends beyond the confines of the baseball field, influencing how businesses and industries leverage data for strategic advantage. By challenging the status quo and implementing innovative strategies, Billy Beane reshaped the game and left an indelible mark on the world of sports and beyond.
Optimising Operations: SMEs and Corrective Action Plans
Corrective measures continue to focus on enhancing process performance or behavior. Generally speaking, you must:
- Identify the process problem – Identify the true nature of the issue. First, confirm that the issue is actually a problem and not just one that is being perceived. If you can formulate the issue as a requirement to compare, also known as a "Should Be" and "Is" statement, that is a good test (e.g. Parts should be nickel plated, parts were received painted black). If you are unable to specify what the desired result should be, you might not have discovered a problem.
- Determine the size of the issue - What is the problem's scope? Verify that you are aware of the scope of the issue. Is it only the product from today, or was yesterday's product also impacted? Is it limited to this particular product, or does it affect others as well? Make sure you are aware of the issue's nature and, more importantly, its absence. This could be crucial information if the issue only occurs on Wednesday.
- Take steps to contain the issue - How can we put a stop to the issue while addressing the underlying cause? Make a change to temporarily solve the issue while you search for and address the root cause. Essentially, what immediate checks or stop-gap measures are you putting in place to ensure that if the problem recurs while you are fixing it, you will definitely catch it?
- Identify the root cause of the problem - What is the source of the problem, not just the symptoms? This is the most difficult part. How do you know you've found the source of the problem? There are numerous approaches to this, ranging from asking "Why" five times until you find the ultimate cause to more difficult methods. There have been entire training courses dedicated to this topic, but suffice it to say that you should try to identify the underlying problem, not just the surface problem. Following this step, it is prudent to ensure that your scope has not expanded, necessitating additional containment actions.
- Create a plan to address the root cause - What do you need to change to eliminate the root cause? Determine what steps are required to eliminate the root cause of the problem. Depending on the problem, you will need to determine the cost and return on investment. How will it be funded (if it is a complicated and costly fix), and who must approve the expense? Check that the planned changes will not cause additional issues.
- Set up your strategy - Carry out your plans. This is as simple as sticking to your plan and seeing it through. It could be as simple as implementing the previously described preventive maintenance program, or as complex as purchasing and installing new equipment because the old one could no longer maintain the accuracy required.
- Verify that your strategy worked - Check to see if your strategy worked. Simply put, after making your changes, wait a reasonable amount of time to ensure that the problem does not reoccur. If it does, you should consider whether you have identified the true root cause. This is the most important step, but it is also the most difficult. People frequently want to complete the paperwork as soon as possible because they believe the registrar requires it to demonstrate timeliness, but proper follow-up is essential.
Types and Examples of Corrective Action
Corrective action in business management can take various forms. Here are some common types of corrective action along with examples:
-
Process Improvement:
- Implementing lean manufacturing principles to reduce waste and enhance production efficiency.
- Introducing automated systems to streamline workflows and eliminate bottlenecks.
- Conducting training programs to enhance employee skills and knowledge.
-
Quality Control:
- Implementing stricter quality assurance measures to reduce product defects.
- Establishing rigorous testing protocols to ensure adherence to quality standards.
- Enhancing supplier management processes to ensure the delivery of high-quality raw materials.
-
Customer Service Improvement:
- Developing a customer feedback system to capture and address customer concerns.
- Providing additional training for customer service representatives to improve response time and problem-solving skills.
- Implementing a customer loyalty program to enhance customer satisfaction and retention.
-
Risk Management:
- Conducting regular risk assessments to identify and mitigate potential threats.
- Implementing robust cybersecurity measures to protect sensitive data.
- Establishing business continuity plans to ensure operations can continue during emergencies or disruptions.
-
Training and Development:
- Providing leadership training to develop managerial skills within the organisation.
- Offering employee development programs to foster professional growth and improve job performance.
- Implementing mentorship programs to facilitate knowledge transfer and skills development.
These are just a few examples of corrective action in business management. The specific types and examples will vary depending on the organisation and the nature of the problem being addressed.
Corrective Measures for SMEs: Strategies for Improvement
Corrective action plays a crucial role in business management due to the following reasons:
- Issue Resolution: Corrective action helps identify and resolve problems within an organisation, preventing them from negatively impacting business operations and outcomes.
- Process Improvement: By analysing the root causes of problems, corrective action allows businesses to identify areas for improvement and implement changes to enhance efficiency and productivity.
- Quality Enhancement: Corrective action ensures that quality standards are met or exceeded by addressing issues that could compromise product or service quality.
- Customer Satisfaction: Taking corrective action demonstrates a commitment to delivering excellent customer experiences, leading to increased satisfaction and loyalty.
- Risk Mitigation: By addressing problems promptly, businesses can minimise risks and prevent them from escalating into more significant issues that could have severe consequences.
- Continuous Improvement: Corrective action is an integral part of the continuous improvement process, enabling organisations to learn from mistakes, make necessary adjustments, and evolve their practices over time.
- Compliance: Corrective action ensures adherence to regulatory requirements, industry standards, and legal obligations, reducing the risk of penalties or legal complications.
Overall, effective corrective action helps organisations maintain a strong competitive edge, improve their reputation, and achieve long-term success in the dynamic business landscape.
How to Take Corrective Action: Effective Procedures for SMEs:
Control measures are crucial for preventing system and procedural failures. In order to safeguard against such occurrences, organisations must adopt various preventive measures. This includes implementing robust quality assurance protocols to ensure accurate and error-free system functionality. Regular system audits should be conducted to identify and rectify any potential vulnerabilities or weaknesses. Additionally, comprehensive backup and recovery mechanisms should be in place to mitigate data loss and system downtime. Adequate training and documentation should be provided to users to ensure proper understanding and adherence to established procedures. Continuous monitoring and evaluation of systems and procedures are vital to identify and address any deviations or non-compliance promptly.
Corrective action in business management involves the following steps:
- Root Cause Analysis: Conduct a thorough root cause analysis to identify the underlying reasons for the failure in policies and procedures.
- Process Improvement: Implement process improvement initiatives to address identified weaknesses and inefficiencies.
- Employee Training and Education: Provide targeted training and education programs to address knowledge gaps and improve employee understanding and compliance.
- Clear Communication: Enhance communication channels to ensure effective dissemination of policy updates and changes.
- Performance Management: Implement performance management systems to monitor and address non-compliance or substandard performance related to policies and procedures.
- Continuous Monitoring and Auditing: Establish regular monitoring and auditing processes to detect and correct any deviations from policies and procedures.
- Corrective Action Plans: Develop and implement corrective action plans to address identified failures and prevent future occurrences.
- Feedback Mechanisms: Create feedback mechanisms to encourage employees to report non-compliance, provide suggestions, and contribute to the improvement of policies and procedures.
- Accountability and Responsibility: Assign clear accountability and responsibility for policy enforcement and ensure that appropriate consequences are in place for non-compliance.
- Leadership Support: Obtain leadership support and commitment to prioritise and invest in the necessary resources for correcting failures in policies and procedures.
To effectively implement corrective action in business management, follow these steps:
- Identify the Problem: Recognise and define the issue or problem that requires corrective action.
- Investigate and Analyze: Gather relevant data, conduct a thorough analysis, and determine the root cause(s) of the problem.
- Develop an Action Plan: Create a comprehensive plan that outlines the specific steps, strategies, and resources needed to address the problem.
- Assign Responsibilities: Delegate tasks and responsibilities to individuals or teams who will be accountable for implementing the corrective action plan.
- Set Timelines: Establish realistic deadlines and milestones to track progress and ensure timely execution of the corrective action plan.
- Implement the Plan: Put the action plan into action by executing the defined strategies and initiatives.
- Monitor and Evaluate: Continuously monitor the implementation progress, measure the effectiveness of the corrective action, and gather feedback.
- Make Adjustments: If needed, make necessary adjustments or modifications to the action plan to improve outcomes and address emerging challenges.
- Document and Communicate: Maintain clear documentation of the entire corrective action process and communicate updates to stakeholders, ensuring transparency.
- Review and Learn: Conduct a comprehensive review of the entire corrective action process, identify lessons learned, and apply those insights to future practices.
By following these steps, businesses can effectively implement corrective action and drive positive change within their organisations.
By following these steps, organisations can effectively address issues, improve processes, and enhance overall performance.
Corrective Action Plan
The corrective action plan is a series of steps designed to solve the problem. The corrective action plan focuses on addressing the underlying cause of the problem rather than simply correcting the symptom that has been identified. When there is a nonconformity, you will take steps to correct it, but what you correct is the difference between a simple correction and a corrective action. A correction will address the most obvious problem, removing the nonconformity and making the process acceptable to continue. This is a correction that may be included in the containment actions.
In contrast, if you look at a problem that has resulted in a nonconformity and investigate the causes of that problem until you understand the cause - which was the beginning of the chain that resulted in the nonconformity (known as the root cause) - and take actions to correct this root cause so that it does not happen again, you have taken corrective action for the problem.
Create a corrective action plan to end the issue once you have determined its underlying cause. When creating your corrective action plan, keep the following in mind:
- Identifying the root cause in its entirety – Have we identified the root cause in its entirety, or could there be another underlying cause to what has been identified?
- The new version of the ISO standards now include a requirement to address the risks and opportunities that are present when you are going to make a change. It has always been important to ensure that the changes you have decided to make won't lead to more issues, but this is now required to be addressed in order to comply with the new standard. Is there a chance, for instance, that changing a process to address a root cause will result in a problem later on in your company or even at your client's location? Is there a chance that once you've identified a good corrective action for one process, you can apply it to other processes to prevent problems from occurring in the future?
- Identify the steps required - What steps are required to remove the root cause from the process?
- Examine the schedule and cost - What is the implementation timeline? What are the costs and expected returns? Are there any other options that should be considered? Is this strategy feasible?
- Plan for ongoing evaluation - Will you need to make changes as you work through your plan? Assessing how well the plan is working as you go can help ensure that your final evaluation of effectiveness yields accurate results.
- Plan for assessing effectiveness - Before we begin the plan, how will we know if the changes were successful? Will one of the key performance indicators improve? Will we have to wait several months to ensure that the problem does not reoccur (which would imply that we did not address the root cause)?
As you can see, the corrective action plan is essentially the same as any other project plan you would create in your organisation. It is critical to set expectations for how long the plan will take, what resources will be needed, and when you will be finished with the corrective action. It is important to note that the ISO standards include a statement that the corrective actions taken should be appropriate to the significance of the effects presented by the nonconformities; thus, it is not expected that you will spend an unusual amount of time and money to address a minor problem. Keep this in mind as you assess the plan's feasibility.
When to Take Corrective Measures
- Identified Non-Compliance: When non-compliance with policies and procedures is identified, whether through internal audits, employee reports, or other means.
- Frequent Errors or Mistakes: When there is a pattern of frequent errors or mistakes occurring due to ineffective policies and procedures.
- Negative Impact on Operations: When the failure of policies and procedures negatively impacts day-to-day operations, productivity, or customer satisfaction.
- Regulatory or Legal Compliance Issues: When policies and procedures fail to meet regulatory or legal compliance requirements, leading to potential penalties or legal risks.
- Customer Complaints or Feedback: When customer complaints or feedback indicate deficiencies in policies and procedures that affect their experience or satisfaction.
- Significant Process Bottlenecks: When policies and procedures create significant process bottlenecks or hinder efficiency and effectiveness.
- Data Breaches or Security Incidents: When policies and procedures fail to adequately address data security, resulting in breaches or security incidents.
- Internal Audit Findings: When internal audits highlight systemic failures or weaknesses in policies and procedures.
- Changes in Business Environment: When changes in the business environment, such as new technologies, industry regulations, or organisational restructuring, render existing policies and procedures outdated or ineffective.
- Evidence of Systemic Issues: When failure in policies and procedures is indicative of systemic issues that require corrective measures to prevent recurrence.
Implementing Corrective Action
It is as simple as following the plan you have identified to implement corrective action. Perform each step you've identified, making sure it's done correctly, and determining whether the changes have introduced new risks that need to be addressed further. Again, thinking of your CA plan as a project plan can help you understand how to proceed with implementation.
When implementing a complex plan, you may want to use a Gantt chart to organise all of the activities, who will do them, and when they will be completed. This type of tool can also indicate which activities can run concurrently and which must wait until other actions are completed. Even if you use another method to track your implementation, it is critical to ensure that actions are labeled with resources, timelines, and status.
Writing a Corrective Action Report
The corrective action report, like any other report in an organisation, can take whatever form is appropriate in your company. Larger companies with a large number of people in top management may require formalized reports for major corrective actions, just as they would for any project. Executive summaries, detailed outcomes and expenses incurred, and evidence of effective closure may all be included in these reports. Others might just include a completed corrective action and preventive action form as the report.
- The nature of the nonconformities for which you have taken corrective action
- The actions taken in corrective action
- The outcomes of corrective actions, including their effectiveness
Remember that the process exists to assist you in saving resources by removing larger systemic problems from your organisation, not to be a burden to your company. Make certain that you implement a corrective action and preventive action system that will benefit you rather than one that is merely decorative. One of the most effective ways to improve your organisation is to eliminate problems.
AEY's Corrective Actions: Swift Solutions in the Face of Adversity
In the adrenaline-fueled world of arms dealing, AEY, led by Ephraim Diveroli and David Packouz, faced a landscape fraught with risks. However, their savvy implementation of corrective and preventative actions showcased a remarkable strategic approach. Picture this: when challenges arose, rather than merely reacting, AEY took a proactive stance, weaving a web of measures to correct course and fortify against potential pitfalls.
When challenges surfaced, AEY didn't shy away. Instead, they implemented corrective actions with precision. Whether it was addressing supply chain disruptions or navigating complex legal terrain, AEY's ability to swiftly rectify issues became a hallmark of their operation. This agile responsiveness allowed them to maintain momentum in the competitive and unpredictable arms industry.
AEY's brilliance extended beyond quick fixes. They understood the value of preventative measures in a high-stakes game. By anticipating potential challenges and implementing proactive strategies, AEY built a fortress against future storms. Whether it was ensuring compliance with regulations or establishing robust risk management protocols, their preventative mindset played a pivotal role in sustaining their operations.
The impact of AEY's corrective and preventative actions reverberates through their legacy. In an industry where volatility is the norm, their strategic approach not only ensured short-term success but also laid the foundation for long-term resilience. Entrepreneurs can draw inspiration from AEY's playbook, recognising that navigating challenges requires a dynamic blend of quick fixes and foresight, turning obstacles into stepping stones in the relentless pursuit of success.
SME Operations: Integrating Preventive and Corrective Actions
The key takeaway from the discussion on implementing corrective and preventative actions in business is a comprehensive understanding of how to enhance operational efficiency and mitigate risks. Firstly, businesses are encouraged to adopt a systematic approach to issue resolution. This involves identifying the root causes of problems through thorough analyses, ensuring that corrective actions are targeted and effective. Clear plans with defined responsibilities and timelines are essential, enabling businesses to monitor progress and address deviations promptly. By proactively managing issues, organisations can maintain a streamlined operation and address challenges at their core.
Secondly, preventative actions play a crucial role in minimising the occurrence of problems. Through continuous risk assessment and anticipation of potential challenges, businesses can implement measures such as quality control processes, employee training programs, and regular equipment maintenance. The emphasis is on creating a proactive culture of learning and improvement within the organisation. This empowers employees to identify and address potential issues before they escalate, fostering a resilient and adaptable business environment.
Lastly, the integration of both corrective and preventative actions into the overall management system is essential for long-term sustainability. By establishing key performance indicators (KPIs) and metrics to monitor processes, businesses can identify early warning signs and take proactive measures. The ultimate takeaway is a strategic and self-sufficient approach to issue management, enabling businesses to optimise their operations, enhance resilience, and ensure sustainable success in the dynamic landscape of business.
Join the Conversation: Share Your Thoughts on This Article
- No comments yet.
Add Your Comment Now!