Guide to Designing and Implementing Quality Management Systems for SMEs
Discover expert tips on designing and implementing effective quality management systems (QMS) to optimise your SME's operations. Enhance quality standards and streamline procedures with practical insights and best practices.
Establishing and maintaining a robust Quality Management System (QMS) is paramount for businesses committed to consistently exceeding customer expectations. This entails a customer-centric approach, involving thorough market research and engagement to understand and integrate customer feedback into product or service design.
Establishing and maintaining a robust Quality Management System (QMS) is paramount for businesses committed to consistently exceeding customer expectations. This entails a customer-centric approach, involving thorough market research and engagement to understand and integrate customer feedback into product or service design.
Business Systems, Policies, and Procedures: Benefits of Quality Management Systems for SMEs
Investing in quality management systems (QMS) is paramount for SMEs striving for excellence. By mastering these systems, SMEs can enhance product/service quality, streamline operations, ensure regulatory compliance, and ultimately bolster customer satisfaction. Learn the vital steps to create tailored QMS frameworks, aligning them with your business objectives and industry standards. With meticulous attention to quality, SMEs can foster a culture of continuous improvement, gain a competitive edge, and pave the way for sustainable growth in today's dynamic market landscape. Take charge of your SME's success by embracing the power of quality
The Crucial Role of Quality Management Systems for SMEs
- Designing and implementing a quality management system (QMS) is crucial for businesses aiming to consistently deliver products or services that meet or exceed customer expectations. Firstly, a thorough understanding of customer requirements and expectations is essential. This involves engaging with customers, conducting market research, and incorporating feedback into the design of products or services. Once customer expectations are clear, businesses can establish quality objectives and performance metrics. A well-defined QMS should outline processes and procedures to ensure quality at every stage of the product or service lifecycle, from design and development to production and delivery. Regular monitoring, measurement, and analysis of key performance indicators are integral to identify areas for improvement.
- Secondly, businesses need to focus on a culture of continuous improvement. This involves fostering a mindset that encourages employees at all levels to actively participate in identifying opportunities for enhancing quality. Training and development programs can equip employees with the necessary skills to contribute effectively to the QMS. Additionally, effective communication channels should be established to ensure that employees are aware of quality objectives and their roles in achieving them. Regular internal audits and management reviews help in evaluating the effectiveness of the QMS and identifying areas for refinement. By embracing a commitment to quality throughout the organisation, businesses can not only meet regulatory requirements but also build a reputation for delivering reliable and high-quality products or services in the market.
How to design and implement quality management system
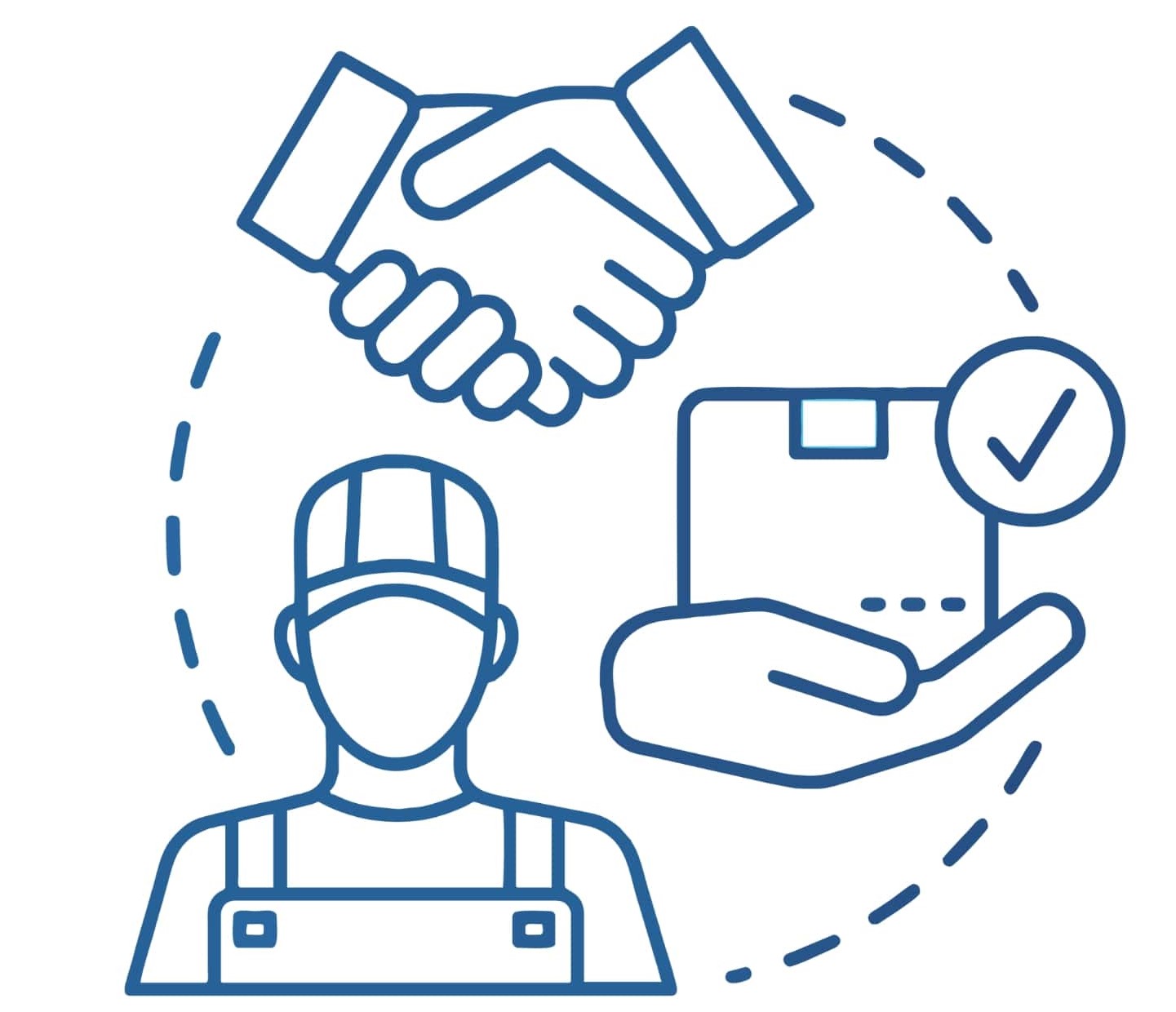
Written by: Malose Makgeta
MBA with 20+ years experience in SME development and funding. LinkedIn Profile
Quality Management System (QMS) - Entrepreneurship Lessons from Movies The Founder, War Dogs and Moneyball
- The Founder (McDonald's): The success of McDonald's can be attributed to the strategic application of quality management principles by the McDonald brothers, Richard and Maurice, and later by Ray Kroc. The brothers revolutionised the fast-food industry by designing a highly efficient and standardized system known as the Speedee Service System. This system emphasized consistency, precision, and a focus on customer satisfaction. Every aspect, from the layout of the kitchen to the preparation of food, was meticulously designed to ensure speed without compromising quality. Ray Kroc, recognising the potential for expansion, played a crucial role in franchising the McDonald's concept. Under Kroc's leadership, the company continued to uphold these quality management principles across its expanding network of franchises. The emphasis on uniformity in processes, strict quality control, and a commitment to customer satisfaction became the cornerstone of McDonald's success, making it a global icon in the fast-food industry.
- War Dogs (AEY): In the movie "War Dogs," AEY, portrayed by David Packouz and Efraim Diveroli, engages in arms dealing rather than implementing a traditional quality management system. The narrative doesn't focus on the ethical or quality control aspects of their business. Instead, the film emphasises the duo's exploits in navigating the complex world of international arms dealing, their involvement in risky ventures, and the challenges they face in meeting the demands of their contracts. The story sheds light on the consequences of their actions rather than showcasing a structured approach to quality management. The film is more centered on the characters' personal and professional dilemmas within the context of arms trading rather than the intricacies of implementing a quality management system.
- Moneyball (Oakland A's): The Oakland Athletics, under the management of Billy Beane, applied innovative and data-driven principles to revolutionise the approach to team management in baseball, as depicted in "Moneyball." Beane and his team embraced the concept of evidence-based decision-making, using advanced statistical analysis to identify undervalued players and maximise the team's performance within a limited budget. This approach, akin to a quality management system in its emphasis on data-driven processes, aimed at achieving consistency and efficiency in player recruitment. By focusing on metrics that were indicative of a player's true value, rather than relying on traditional scouting methods, the A's successfully challenged conventional norms in the baseball industry. The application of this systematic, analytics-based approach not only transformed the A's into a competitive force but also had a profound impact on the broader landscape of sports management, showcasing the power of strategic, data-centric decision-making.
- Explore further insights on How to implement systems and procedures derived from our case study movies: The Founder, War Dogs and Moneyball by clicking here.
CONTEXT
Management control, systems, and procedures hold managers accountable for an organisations performance. System and procedures ensure that entrepreneurs and business managers meet customers expectations and improve the brand of the business, both of which are critical to the growth of a healthy business. Management control, system, and procedure are all management functions that aid in the detection of errors and the implementation of corrective actions. This is done to reduce deviation from standards and ensure that the organisations stated goals are met in the desired manner. This skills programme provides a platform and tools for entrepreneurs and business managers to create business systems and procedures in minutes.
Description
The QMS design is influenced by the organisation’s varying objectives, needs, and products and services provided. A quality management system (QMS) is a set of policies, processes and procedures required for planning and execution (production/development/service) in the core business area of an organisation
Purpose
Be able to design and build portions serve to develop the structure of a quality management system, its processes, and plans for implementation to be able to safeguard the business its reputation, accelerate change, and satisfy customer needs, it must be able to design and build portions that serve to develop a quality management systems structure, processes, and plans for implementation.
Rational
Quality management system is an integrative element, uniting diverse aspects of a business into a unified purpose of delivering products/services in their best form.
Key Lessons
Click here and draft your business plan in minutes
To request tailored accredited training and enterprise development services, contact us at businessplan@superdealmaker.com.
Get List for Funding Opportunities in Minutes, Click Here
To request tailored investment banking services, contact us at businessplan@superdealmaker.com.
Benefits of Quality Management Systems: McDonald's, Moneyball, and War Dogs
McDonald's: Golden Arches of Global Fast Food
McDonald's, the epitome of the fast-food industry, revolutionised the business landscape with its franchise model. Founded by Ray Kroc and inspired by the McDonald brothers, the company thrived on standardized processes, efficient service, and a customer-centric approach. Its success lay in scalability, turning a small idea into a global phenomenon through the power of franchising. Key lessons: innovation, adaptability, and maintaining a consistent customer experience.
Moneyball: Data-Driven Triumph in Baseball
The Oakland Athletics, under Billy Beane's leadership, defied baseball conventions with Moneyball. Their business was baseball, and their product was a winning team. Implementing a Quality Management System (QMS), the A's shifted from traditional scouting to data-driven decision-making. Their success lay in efficient resource allocation, leveraging statistics to assemble a competitive team on a limited budget. The impact was transformative, influencing not only the A's but the entire baseball league. Key lessons: unconventional strategies, resource optimisation, and the ripple effect of innovation.
War Dogs: Arms Dealing in the Shadows
War Dogs, a tale of entrepreneurship in the arms industry, features Ephraim Diveroli and David Packouz. Unlike the other two, this business operated in the shadows of government contracts. Their success lay in seising opportunities and navigating ethical complexities. War Dogs highlights the importance of aligning passion with the venture but also raises questions about ethics in business. Key lessons: entrepreneurial spirit, risk management, and the ethical considerations of navigating a controversial industry.
Quality Management Systems: A Game Changer for SMEs
A Quality Management System (QMS) is a set of policies, processes, procedures, and resources that are implemented within a business to ensure consistent quality in its products or services. It is designed to meet customer requirements, enhance customer satisfaction, and continuously improve business operations.
QMS is defined as a formalized system that documents processes, procedures, and responsibilities for achieving quality policies and objectives.An organisation's activities can be better coordinated and directed with the aid of a QMS, which also helps it continuously increase its effectiveness and efficiency while adhering to customer and regulatory requirements.
The most popular method for quality management systems is ISO 9001:2015, an international standard that details the specifications for quality management systems. Although some people mistakenly use the term "QMS" to refer to the ISO 9001 standard or the collection of documents outlining the QMS, it actually refers to the entire system. Only the system's description is provided by the documents. A QMS typically follows the principles outlined in international standards such as ISO 9001, which provides a framework for establishing, implementing, maintaining, and continually improving an effective quality management system.
Detailed Components of a Quality Management System (QMS)
A Quality Management System (QMS) consists of various components that work together to ensure consistent quality and continuous improvement within a business. Here are the detailed components of a QMS:
- Quality Policy:A documented statement that outlines the business's commitment to quality, including its objectives and principles.
- Quality Planning:The process of establishing quality objectives, determining the necessary resources, and developing a plan to meet those objectives. It involves identifying customer requirements, setting quality targets, and defining processes to achieve them.
- Quality Control:The activities performed to ensure that products or services meet specified requirements. This may involve inspections, testing, and monitoring of processes to detect and address quality issues.
- Quality Assurance:The systematic actions taken to provide confidence that quality requirements will be fulfilled. It involves planning, implementing, and evaluating quality systems, including the establishment of processes, procedures, and standards.
- Quality Improvement:The continuous effort to enhance performance, processes, and systems based on the analysis of data and customer feedback. It involves identifying areas for improvement, implementing changes, and monitoring the results to drive ongoing progress.
- Documentation:The creation and maintenance of documented information such as quality manuals, procedures, work instructions, and records. This ensures that processes are standardized, communicated effectively, and can be consistently followed.
- Training and Competence:Ensuring that employees have the necessary skills, knowledge, and training to perform their tasks effectively and contribute to quality. This involves providing training programs, assessing competency, and promoting a learning culture.
- Audits and Reviews:Regular assessments and evaluations of the QMS to identify areas for improvement and ensure compliance with established processes and standards. Internal audits and management reviews are conducted to monitor performance and drive accountability.
- Customer Focus:Placing the customer at the center of quality management efforts. This involves understanding customer needs, gathering feedback, and incorporating customer requirements into product design, service delivery, and overall business processes.
By implementing and effectively managing these components, businesses can establish a robust QMS that promotes quality, drives continuous improvement, and enhances customer satisfaction. It serves as a framework to guide the organisation in delivering products or services that consistently meet or exceed customer expectations.
Effectiveness of Quality Management System
The effectiveness of the implemented QMS is determined by a number of factors, the most important of which are:
- Senior management's commitment to monitoring, controlling, and improving quality. Senior management must be heavily involved in quality management activities, beginning with the development of an organisational quality strategy.
- Motives for adopting the standard. Internal motivations such as a genuine desire to improve product quality, company processes, and process efficiency tend to facilitate and increase the effectiveness of the standard's implementation.
- Making a convenient analysis of the company's internal context that wants to adopt the standard, preparing for standard implementation (e.g. training), planning for standard implementation in the organisation, and organisational receptivity to standard implementation (personnel, culture).
- The extent to which the standard has been effectively implemented (i.e., internalisation of the standard in the processes of the organisation).
- The extent to which the QMS focuses on improving the customer experience. The most general definition of quality is "whatever the customer perceives to be good quality." This means that a company does not have to make a product that never fails; some customers are more tolerant of product failures if they always receive shipments on time or have a positive experience in another aspect of customer service.
The Blueprint for Excellence: McDonald's Implementing a Stellar Quality Management System
McDonald's, a global giant in the fast-food industry, didn't ascend to its throne by chance. One key ingredient in its recipe for success lies in the meticulous implementation of a robust Quality Management System (QMS). Recognising the imperative of delivering a consistent and high-quality dining experience, McDonald's strategically embraced a comprehensive QMS. This system, akin to a carefully crafted recipe, outlines the standards and processes crucial for maintaining the quality that customers around the world have come to expect from the Golden Arches.
McDonald's unwavering commitment to its QMS has had a profound impact on both its operations and customer satisfaction. By implementing stringent quality control measures, McDonald's ensures that each Big Mac, every french fry, and all beverages meet the same high standards across the globe. This not only guarantees a consistent taste but also reinforces the trust customers place in the brand. The impact of a well-implemented QMS extends beyond the menu—it permeates the entire McDonald's experience, from cleanliness to service, elevating the brand to a standard of excellence.
So, how did McDonald's ensure the seamless implementation of its QMS? The answer lies in meticulous attention to detail. From supplier audits to staff training programs, each element of the QMS was woven into the fabric of McDonald's operations. The company embraced technology for real-time monitoring, ensuring immediate corrective actions when deviations occurred. This commitment to continuous improvement not only upheld quality but also positioned McDonald's as an industry benchmark for operational excellence. It's a lesson for businesses: a well-implemented QMS isn't just a checkbox; it's a philosophy that permeates every aspect of your organisation, fostering a culture of excellence.
As the world changes and consumer expectations evolve, McDonald's continues to adapt its QMS to maintain its high standards. The impact of this commitment reverberates not only in the satisfaction of millions of customers but also in the enduring success of the McDonald's brand. So, whether you're flipping burgers or managing a multinational corporation, the McDonald's journey into quality management serves as a beacon—a reminder that excellence isn't a one-time achievement but a continuous journey.
Effective Quality Management Essential Principles
The ISO 9001 certification is built on the 8 Principles of Quality Management, which were developed by ISO/TC 176, an international organisation responsible for maintaining ISO's quality management standards. These principles will steer your quality management programmein the right direction for Businesses looking to improve their performance.
Customer Focus
This should almost go without saying. A company that does not prioritise its customers will not last long. Although customer focus is essential, it is often overshadowed by the priorities of a quality system and the various processes involved.
Customers, both current and prospective, should be prioritised. Companies should measure customer satisfaction in addition to meeting or exceeding customer expectations on a continuous basis. Failure to meet customer expectations, on the other hand, should be tracked. Every function and department should participate.
Customer focus is, as expected, the first principle, and it should be. It addresses both customer requirements and customer service. This principle emphasises the importance of a company understanding its customers, what they require, and when they require it. While attempting to meet, if not exceed, customer expectations.
As the company's ability to identify and satisfy new customer opportunities improves, so does customer loyalty, revenue, and waste. Improved customer satisfaction results from more efficient processes.
Leadership
As with any good idea, support must begin at the top. An organisation will suffer if it lacks good leadership. Leaders should establish a company vision and goals.
Consider an inspiring leader you've met. This could have happened at work or at a quality event.
The organisation's direction - The company should have clear goals and objectives, and its employees should be actively involved in achieving those goals.
The benefits include increased employee engagement and motivation to meet customer needs. Employees are more productive when they are kept "in the loop" and understand the business vision, according to research. This principle seeks to rectify employees complaints about 'lack of communication'.
Engagement of People
You want to have a workforce that is engaged. This indicates that the staff's skills are utilized and valued. Additionally, it promotes learning, discussion, and ongoing improvement. Employees who are held accountable for their actions have an engaged workforce. The job demands that everyone in the organisation be active and engaged in their work, as opposed to being seen as a passive place to clock in every morning.
The process approach is all about efficiency and effectiveness - Well-managed processes reduce costs, improve consistency, eliminate waste and promote continuous improvement.
By becoming a more efficient organisation, you will build confidence in your stakeholders by optimising performance. Manage processes by making responsibilities clear and ensuring your resources are used in the best way.
Process Approach
A process approach lays out the steps for success, as it does with so many other aspects of quality. This implies that activities are measured, managed as processes, and relationships between activities are found. Improvement possibilities are monitored. It takes effort to produce quality. Behind-the-scenes procedures are necessary to guarantee the organisation's success.
The process approach focuses on efficiency and effectiveness. It is also about consistency and understanding that good processes accelerate activities.
Great processes save money, increase consistency, eliminate waste, and encourage continuous improvement.
Systematic Approach to Management
“Identifying, understanding and managing interrelated processes as a system contributes to the organisation’s effectiveness and efficiency in achieving its objectives.”
A business focuses its efforts on the key processes as well as aligning complementary processes to get better efficiency. This means that multiple processes are managed together as a system which should lead to greater efficiency.
Improvement
A process approach lays out the steps for success, as it does with so many other aspects of quality. This implies that activities are measured, managed as processes, and relationships between activities are found. Improvement possibilities are monitored. It takes effort to produce quality. Behind-the-scenes procedures are necessary to guarantee the organisation's success.
This principle is simple: continuous improvement should be an active business goal.
The advantages are obvious: increased ability to seize new opportunities, organisational flexibility, and improved performance. Businesses that can adapt to new market situations thrive, especially in difficult economic times.
Evidence-Based Decision-Making
Gut instincts are not a good way to proceed, as you might have guessed. The king is actually data. For a competent professional, this should come as no surprise. The accessibility, reliability, and accuracy of data should be ensured by Businesses. Decisions need to be made based on its analysis. However, it is important to balance data analysis with real-world experience. But it's important to remember that experience is just as important as the numbers.
A logical approach based on data and analysis makes good business sense. Unfortunately, in a fast-paced workplace, decisions are frequently made rashly and without proper thought. Implementing the Quality Management Principles we've discussed will allow for more informed decisions.
As data is collected and analyzed, informed decisions lead to a better understanding of the marketplace and the ability to defend previous decisions.
Relationship Management
The relationships between suppliers and other partners are crucial, and people are always the most important component of any organisation. Suppliers should be carefully chosen based on their capacity to both add value and control costs. Plans and information that would aid partners in their work should be shared with them. The intention should be one of cooperation. Both parties can benefit from coordinating improvement initiatives. Maintaining a strong relationship with a supplier will also be greatly aided by acknowledging their achievements.
This principle is concerned with supply chains. It promotes the company's relationship with its suppliers, recognising their interdependence. A strong relationship boosts productivity and promotes smooth working practices.
As a result, costs and resources are optimised, long-term relationships are improved, and 'flexibility of joint responses to changing markets or customer needs and expectations' is achieved.
Most people would agree that quality is important but difficult to achieve. Among the many tools at your disposal, a quality management system (QMS) can provide a road map to higher quality. A company would be lost without it.
The Ripple Effect of QMS: The Oakland Athletics Implementation of Quality Management
In the realm of baseball, the Oakland Athletics, under the visionary leadership of Billy Beane, redefined the game with an unconventional approach known as Moneyball. At its core was the implementation of a robust Quality Management System (QMS). Instead of relying solely on traditional scouting methods, the A's embraced data-driven decision-making. This strategic shift meant meticulous data collection, rigorous analysis, and the identification of undervalued players based on statistical performance rather than conventional wisdom.
The A's adoption of a Quality Management System was a strategic response to the limitations of traditional scouting. In a game where resources were finite, the QMS allowed the A's to allocate their budget efficiently and maximise player performance. This method, while initially met with skepticism, proved to be a game-changer. By focusing on statistical indicators of player success, the A's could assemble a competitive team without breaking the bank on high-profile players. It was a revolution in baseball strategy that showcased the power of meticulous quality management.
The impact of the Quality Management System at the A's was nothing short of transformative. Beyond the individual player choices, it altered the landscape of baseball strategy. The A's demonstrated that a systematic, data-driven approach could not only compete with but outperform traditional methods. This success resonated across the league, influencing how other teams approached player recruitment and team building. The A's had not only crafted a winning formula for themselves but had ignited a league-wide revolution in the way baseball teams managed and optimised their resources.
Quality Management Principles for Sustainable Success: Importance of Implementing QMS for a Business
A Quality Management System (QMS) offers numerous benefits to a business, making it a valuable investment. Here are some key reasons why implementing a QMS is important:
- Improved Product/Service Quality: A QMS helps businesses maintain consistent quality in their products or services, leading to increased customer satisfaction and loyalty.
- Enhanced Customer Satisfaction: By consistently meeting customer requirements and expectations, businesses can improve customer satisfaction levels, resulting in repeat business and positive word-of-mouth referrals.
- Efficiency and Cost Savings: Implementing a QMS helps identify and eliminate inefficiencies, reduce errors, and minimise waste and rework. This leads to cost savings and improved overall efficiency in business operations.
- Better Decision-Making: A QMS provides businesses with access to accurate and reliable data about their processes, allowing for informed decision-making and strategic planning based on evidence.
- Compliance with Regulations and Standards: Many industries have specific regulations and standards that businesses must adhere to. A QMS helps ensure compliance with these requirements, reducing the risk of penalties, legal issues, and reputational damage.
- Continuous Improvement: QMS promotes a culture of continuous improvement by encouraging regular reviews, audits, and corrective actions. This enables businesses to identify areas for enhancement and implement changes to drive ongoing progress.
- Competitive Advantage: Implementing a QMS demonstrates a commitment to quality and customer satisfaction, setting a business apart from competitors. It can serve as a competitive advantage in attracting new customers and retaining existing ones.
- Employee Engagement: A well-implemented QMS engages employees by providing clear processes, roles, and responsibilities. It fosters a sense of ownership, teamwork, and pride in delivering high-quality products or services.
- Risk Management: A QMS incorporates risk management practices, allowing businesses to identify, assess, and mitigate risks proactively. This helps prevent quality-related issues, product recalls, and customer dissatisfaction.
By implementing a QMS, businesses can achieve these benefits and establish a culture of quality, continuous improvement, and customer focus. It is a strategic investment that can contribute to long-term success and sustainability.
Advantages of Quality Management System
Proper quality management can benefit business by increasing investment, market share, sales growth, sales margins, competitive advantage, and avoiding litigation.
- Businesses can define who is affected by their work and what they expect by assessing their context. This allows for clearly stated business goals as well as the identification of new business opportunities.
- Businesses can identify and address the risks that are associated with them.
- Businesses can ensure that they consistently meet customer needs and improve customer satisfaction by putting customers first. This can result in more repeat customers, new clients, and increased revenue for the company.
- Businesses operate more efficiently when all of their processes are aligned and understood by all. This increases productivity and efficiency while lowering internal costs.
- Businesses will meet statutory and regulatory requirements while expanding into new markets, as some sectors and clients require a qms before doing business.
Disadvantages of Quality Management System
- The amount of money, time, and paperwork required for a complete implementation
- Opponents claim that QMS is only for documentation
- QMS only promotes specification, control, and procedures rather than understanding and improvement.
- QMS is prone to failure because businesses are interested in compliance rather quality management
How to Implement of Quality Management System
Your company must recognise and oversee numerous interconnected, multifunctional processes before implementing a quality management system to help guarantee customer satisfaction. The various objectives, needs, and goods and services offered by the organisation should be taken into consideration when designing the QMS. This structure is based largely on the plan-do-check-act (PDCA) cycle and allows for continuous improvement to both the product and the QMS. The following are the fundamental actions in putting in place a quality management system:
- Design and Build - A QMS's structure, processes, and implementation plans are developed during the design and build phases. Senior management should be in charge of this area to make sure that the organisation's and its customers' needs are what motivates the development of the systems.
- Deploy - The best way to deploy is to break each process down into subprocesses and train staff on documentation, education, training resources, and metrics. Utilising company intranets to help with the implementation of quality management systems is becoming more and more common.
- Control and Measurement – Routine, systematic audits of the quality management system are a key component of establishing control and measurement, two aspects of a QMS. Depending on the size, potential risk, and environmental impact, the specifics vary greatly from organisation to organisation.
- Review and Improve - Examine and refine the processes used to handle audit results. The objectives are to assess the efficiency and effectiveness of each process in relation to its goals, to share these conclusions with the staff, and to create new best practices and processes based on the information gathered during the audit.
QMS Implementation Plan - Process Approach
- Plan - Determine system flaws and create a plan. Decide what procedures and clauses the QMS needs. Determine which of the processes that make up your management system is in charge of fulfilling which requirements, as well as any gaps.
- Do - Put changes in place and raise awareness. Developing and documenting current processes and procedures is an essential component of a QMS. Concentrate on developing and implementing processes and procedures that cover the essential QMS activities.
- Check - Ensure that the changes have been implemented. Use the audit program and audit checklists to conduct an elemental internal audit of selected functions and areas. Ensure that the auditors do not audit their own functions or processes.
- Act - Take action in response to the audit findings. Corrective actions should be taken by the process owners in response to the audit findings. The Monitoring verifies documented corrective actions before final approval.
Assign Resources and Budget
Top management must ensure that the necessary resources and funds are available to support the implementation of the quality management system. The formal endorsement and commitment of top management is the first critical step in the development and implementation of any management system.
The proposed quality management system development and implementation should be formally documented, approved, and include the proposed implementation strategy, a broad timeline, and an estimated budget.
The appointment of a professional Quality Manager or 'Management Representative' is a critical factor in the successful implementation of a quality management system. It is strongly advised that a full-time senior member of staff be appointed; it is advantageous for the implementation process if they are familiar with your company.
Adopt the Standards
Determine which processes and clauses are required for the quality management system. Determine which processes are responsible for meeting which requirements by identifying the processes that comprise your management system. Determine which processes are responsible for meeting which requirements by identifying the processes that comprise your management system.
You should concentrate on two types of processes. Key processes are the steps you take to give the customer what they want, such as from order acceptance to design to delivery, whereas support processes are those that do not directly contribute to what the customer wants but do assist the key processes in achieving it. Human resources, training, and facility maintenance are examples of support processes.
Consider how workflows flow through your organisation as a good starting point. Consider how the key processes' inputs and outputs flow from one to the next, what sub-processes may exist within it, and how the support processes interact. For the time being, disregard the standard; in fact, put it in a drawer and forget about it. Instead, concentrate on your key processes and how departments interact with one another.
Form the Quality Management System Implementation Team, which will conduct the gap analysis in Step 3. An introductory training session for all staff involved in the quality management system should be organised, beginning with the quality management system Implementation Team and top management.
Gap Analysis and Action Plan
A gap analysis is a technique to clearly identify which quality management processes are currently not being fully addressed (or not addressed at all) and to develop remedial actions.
The unique knowledge gained about the current state of your quality management system will be the primary driver of the subsequent implementation strategy. Armed with this knowledge, you can create accurate budgets, resources, timelines, and expectations that are proportional to the state of your current management system when compared to the new standard's requirements.
A gap analysis exercise will help you identify the differences, or gaps, between your current management system and the new requirements. Prepare the findings and create a gap analysis action plan that includes tasks/actions, deliverables, owners, and timeframes. Before proceeding, submit to the Management Representative for approval.
Begin Closing the Gaps
Once the gaps in the system have been identified and a committed implementation team has been formed, it is now possible to develop an achievable and manageable gap implementation plan that identifies the resources required to fill the gaps. The gap implementation plan should prioritise the correction of noncompliant processes based on the results of the gap analysis.
A good plan is frequently the key to any successful project, and projects that lack a plan tend to run indefinitely and without demonstrating measurable progress. You have specific deadlines to meet if you have a plan.
Select and Train Internal Auditors
Begin internal auditor training by selecting external training providers. Top Management and the Management Representative will meet to discuss the internal auditing requirements. It is planned to train internal auditors on how to audit a QMS.
Begin Internal Auditing
Using the audit program and audit checklists, conduct an elemental internal audit of selected functions and areas. Make sure the auditors are not auditing their own functions or processes.
During the implementation phase, conduct one or two system audits that cover all of the requirements applicable to your quality management system. All employees should be given sufficient resources and lead time to prepare for the audit and implement any subsequent corrective actions.
Prepare a narrative for each section of the internal audit report, as well as copy and paste trend tables and charts to summarize your findings. Ascertain that the audit report has been reviewed and approved. Submit the audit report for review and action to top management.
Once the quality management system is complete and everyone is using it, you should audit each key process. Begin by identifying a key process and its inputs and outputs.
Implement Corrective Actions
Carry out the corrective actions outlined in the previous step. Corrective actions should be taken by the process owners in response to the audit findings. The documented corrective actions must be submitted for approval to the Management Representative.
Once the new key requirements have been implemented and any corrective actions have been addressed, it is recommended that businesses conduct at least one additional internal (element) audit in accordance with the defined milestones established by the implementation plan.
Management Review
Conduct the third management review. Top management will review the current gap analysis action plan results, identify areas of weakness, prioritise any issues identified, and authorize corrective action as needed.
- Quality objectives and performance indicators; Verification of completed corrective actions;
- Internal audit results and analysis
- The outcomes of the core QMS processes and procedures that were developed and implemented.
Top management should ensure that any negative management review findings are addressed. Change the quality management system and the documentation information as needed.
Certification Body Audit
Audit findings are addressed by the Certification Body (this could be your own board). The organisation should coordinate with the certification body to set audit dates that are convenient for all parties. All employees should be given enough time to prepare for the certification audit. All documentation required for the audit should be easily accessible.
Top management should ensure that any negative audit findings are corrected as soon as possible. Change the quality management system and the documentation information as needed. To ensure a successful re-audit, the Management Representative should address the issues raised by the Certification Body.
Verification and Certification
It is imperative that the achievement of quality management certification of compliance. Quality management requires Businesses to ‘continually improve the effectiveness of the quality management system and its process
Even when producing conforming products, processes can always be made more efficient and effective. A continuous improvement program's goal is to identify areas for improvement in order to increase the likelihood of customer satisfaction. It requires the organisation to plan improvement systems and consider a variety of other activities that can be used in the improvement process. These are typically the results of data analysis.
You will be expected to continuously improve the degree to which your products and services meet customer requirements, as well as to measure the effectiveness of your processes. To that end, the principle of continuous improvement implies that you should adopt the mindset that improvement is always possible, and that Businesses should develop the skills and tools required to drive improvement.
Quality Management Journey: Unraveling the Quality Quandary at AEY
In the tumultuous world of arms dealing, the AEY Inc. saga, as portrayed in War Dogs, takes a gripping turn when confronted with the need for a robust Quality Management System (QMS). Picture Ephraim Diveroli and David Packouz navigating the complexities of government contracts and international regulations with a seat-of-the-pants approach. As their ventures expanded, the lack of a structured QMS became increasingly apparent, leading to a series of missteps and near-calamities.
Recognising the imperative for change, AEY embarked on a mission to implement a Quality Management System. This involved a comprehensive overhaul of their operational processes, from procurement to delivery. Embracing industry best practices, they introduced standardized procedures, stringent quality checks, and documentation protocols. The implementation wasn't without its challenges—navigating the murky waters of the arms trade while adhering to international standards required finesse and adaptability.
The adoption of a Quality Management System at AEY ushered in a paradigm shift. Beyond mere compliance, it became a catalyst for efficiency and credibility. The systematic approach to quality assurance not only mitigated risks associated with the arms business but also instilled confidence among clients and partners. AEY transformed from a risky player in the arms market to a more reliable and compliant contractor, navigating the complexities of international arms trade with newfound legitimacy.
Entrepreneurs, take note. AEY's journey underscores the importance of proactively implementing a Quality Management System, especially in industries where compliance is non-negotiable. Start by assessing your operational vulnerabilities, then craft a tailored QMS that aligns with industry standards. Remember, the impact goes beyond mere adherence to regulations—it can redefine your reputation and open doors to opportunities previously inaccessible.
Quality Management Principles: Building a Culture of Quality
The key takeaway from the discussion on designing and implementing a Quality Management System (QMS) is the critical role it plays in ensuring businesses consistently meet or exceed customer expectations. To achieve this, businesses must adopt a customer-centric approach by actively engaging with customers, conducting thorough market research, and incorporating valuable feedback into the design of their products or services. The establishment of clear quality objectives and performance metrics at every stage of the product or service lifecycle is paramount, ensuring a structured and standardized approach to maintaining high standards.
Furthermore, the importance of fostering a culture of continuous improvement within the organisation cannot be overstated. This involves empowering employees at all levels with the skills and mindset necessary to actively contribute to enhancing quality. Training programs, effective communication channels, and regular internal audits are essential components in this ongoing process of refinement. The commitment to quality, when embedded throughout the organisational culture, not only ensures compliance with regulatory standards but also positions the business as a reliable and high-quality provider in the market.
Ultimately, businesses that invest in a robust QMS not only enhance their reputation but also gain a competitive edge. The takeaway emphasises the significance of quality assurance in building customer trust, improving market visibility, and establishing a strong foundation for sustainable growth and success.
Join the Conversation: Share Your Thoughts on This Article
- No comments yet.
Add Your Comment Now!